Steam engine
A steam engine is (in the narrow sense) a reciprocating thermal engine. Water is vaporized in a heated steam generator, which is considered a component of the machine. The pressurized steam converts the heat energy (also pressure energy) it contains into kinetic energy by moving a piston that moves in a cylinder. Typically, the piston is part of a thrust crank mechanism that converts the reciprocating motion of the piston into rotation of a flywheel that drives the prime mover. To reverse the motion of the piston, the pressure is deflected to the other cylindrical side of the piston.
Another steam-driven heat engine is the steam turbine, which converts the thermal energy of the steam into rotational energy without the need for a follow-up mechanism (gearbox) to change the mode of motion.
Steam engines are heat engines with "external combustion", which distinguishes them from internal combustion engines.
The applications of Thomas Newcomen's first functioning steam engine were found from the beginning of the 18th century in coal mining for dewatering, where they initially supplemented and later also replaced older mechanical power sources such as water wheels. After gradual improvements in efficiency, it became worthwhile towards the end of the 18th century to use them in the growing textile industry to drive textile machines, and they eventually spread to other branches of industry, where they also supplemented water and windmills. A decisive improvement was achieved by James Watt, who received a patent for it in 1769. In the course of the 19th century, they gained an important role in transportation, especially for powering steamships and steam locomotives. Their use as locomobiles was also not insignificant. After initial successes, their use in steam automobiles and trucks lost importance and practically no longer exists today. The situation is similar in the field of steam tractors and locomobiles, where steam propulsion dominated before 1900. The first airship was also powered by a steam engine in 1852. At the turn of the 20th century, steam engines were generally replaced by the electric motor and, as a vehicle drive, by the internal combustion engine. Steam turbines are still used today in power plants to generate electrical energy.
The following article deals only with reciprocating engines (steam engines "in the narrow sense").
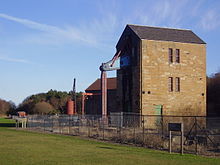

Pump house of a water lifting steam engine with balancer and pump rods
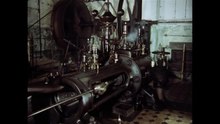

Play media file Video: Cylinder steam engine in a linen weaving mill, 1981
.gif)

Animation of a double-acting steam engine with centrifugal governor
Mode of operation of a piston steam engine
The piston steam engine converts thermodynamic energy (steam pressure) from steam generators into mechanical rotational energy. In the process, a piston moves back and forth in the associated cylinder, performing an oscillating motion. However, a rotational movement is usually required for the useful mechanical energy.
The outward movement of the piston is carried out with the pressure of the steam as a power stroke. The return movement of the piston is performed from stored rotational oscillation energy when the piston is pressurized on one side. In the case of a piston pressurised on both sides, however, the return movement of the piston is also performed as a power stroke, but now on the underside of the piston using steam pressure control.
The steam supply into the cylinder is controlled by a slide valve. The piston is first moved downwards or in the direction of the crankshaft with the pressure. The linear movement of the piston is converted into a rotational movement by means of a crosshead and connecting rod as a coupling element on the crankpin of the crankshaft. The connecting rod then (in one-sided operation) uses the rotational energy stored in the flywheel and crankshaft to push the piston linearly back from the lower position to its upper starting position.
The working process of a steam engine is thus divided into two cycles and is therefore a two-cycle process.
Atmospheric steam engine
In an atmospheric steam engine, the cylinder space under the piston is filled with steam. In the next working cycle, water is injected into the cylinder so that the water vapour cools down and condenses in the process. A vacuum is created so that the piston is forced into the cylinder by the external atmospheric pressure. The extending movement of the piston takes place with the steam valve open and by means of a flywheel mass attached to a lever arm, the so-called balancer.
The best-known representative of this design was the atmospheric steam engine by Thomas Newcomen from 1712. The steam engine was mainly used for keeping water in coal mines. The energy efficiency of this engine was less than 1 % until it was further developed by James Watt. Watt transferred the condensation of the steam from the working cylinder to a downstream water-cooled container, the condenser. This eliminated the need to constantly cool and reheat the working cylinder in each working cycle, a cause of considerable energy losses.
The illustration on the right shows how the negative pressure or atmospheric pressure in the atmospheric steam engine does the work when the hot steam condenses and contracts sharply. Most of the water that comes out of the cylinder is liquid. This method of operation is not very economical, as much energy is used in heating and cooling the cylinder and piston at each cycle. To allow the steam to condense quickly enough, cold water was injected into the cylinder near top dead center (not shown here).
In the expansion steam engine, the fill valve opens only briefly at the beginning of the cycle. In contrast to the full pressure machine, the steam flowing in under high pressure loses part of its pressure during the working cycle. Although this also leads to a cooling of the cylinder, considerably less steam is consumed than with the full pressure machine. To limit cooling, the steam is not completely expanded to atmospheric pressure. Compound steam engines also take advantage of the pressure remaining when the steam exits by directing the steam into another cylinder of larger diameter. (Note: Contrary to what is shown here, the steam hardly cools any further during the downward movement of the piston).
Low pressure steam engine
In the low-pressure steam engine, the steam is applied at a slight overpressure of a few 100 mbar. In contrast to the Newcomen steam engine, work is done not only during condensation but also during filling of the cylinder. This leads to an increase in efficiency and was the starting point for the further development of the steam engine to higher steam pressures. The best-known representatives of this design were the steam engines of James Watt from about 1769 (see below).
Watt also developed the single-acting steam engine, which acted on the piston from one side only, into a double-acting steam engine, in which the piston was acted on alternately from the top and bottom. This resulted in a reduction in mass and also increased efficiency and output to a certain extent, as the idle stroke was eliminated.
High pressure steam engine
In high-pressure steam engines, the steam is heated to well over 100 °C, so that a higher pressure builds up. Cooling of the steam leaving the cylinder can be dispensed with, as the atmospheric pressure is no longer a factor compared to the significantly higher operating pressure (exhaust operation). The condenser can thus be dispensed with, which, in conjunction with the higher energy density of the pressurised steam, makes this type of engine considerably lighter and thus made the use of steam engines in steam locomotives possible in the first place. Representatives of this type are practically all piston steam engines in vehicles since Oliver Evans and Richard Trevithick from about 1802 (see below). High-pressure steam engines also made it possible to use steam expansion. Whereas atmospheric and low-pressure steam engines are usually full-pressure engines with steam flowing into the cylinders during the entire piston stroke, the cylinders of an expansion engine only receive steam at the beginning of each piston stroke. Further movement is caused by the expansion of the steam as the pressure falls. The energy stored in the steam is thus utilized much better
Compound Steam Engine
A compound steam engine or multiple expansion engine is a steam engine with at least two working units connected in series in the direction of steam flow.
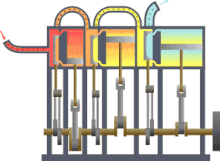

Schematic of a triple expansion steam engine
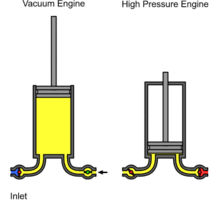

Comparison between atmospheric steam engine (left) and expansion steam engine (right)
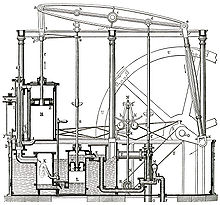

steam engine
Steam engines today
As a vehicle drive, steam engines have largely been replaced by internal combustion engines, which start without warm-up time, are more efficient, offer greater power with less weight and are more convenient to operate. Furthermore, due to the widespread supply of electrical energy, the steam engine has lost its function as the central energy source of an industrial enterprise, which it held for a long time. In coal mining, steam engines were and still are used in hoisting plants, for there the steam engine can serve both as a hoisting machine for lifting coal and as a brake for lowering backfill material. When braking, the energy is used to heat the steam.
Although the era of the piston steam engine seems to be long gone, a renaissance is not out of the question. One of its advantages over the internal combustion engine is its continuous combustion process, which can be designed with lower emissions. Another advantage of the steam engine is its extreme overload capacity when power peaks are demanded. The closed circuit of steam and feed water, which is common today, results in low-emission lubrication of the engine's cylinder and piston. In this sense, the steam engine has been developed as a modernized steam engine.
In the late 1990s, IAV GmbH was commissioned by Volkswagen AG to develop such a modern "steam engine", which uses extremely low-emission external combustion to generate a certain supply of high-pressure steam, which is then injected via nozzles according to energy requirements, as in a diesel engine. At the end of 2000, this gave rise to the company Enginion, which further developed the current SteamCell from the ZEE (Zero Emission Engine) prototype, which achieved an efficiency of 23.7%. This engine operated in a two-stroke process and also managed without the usual lubricants because the wearing parts were made of modern carbon components. However, Enginion had to file for insolvency in 2005.
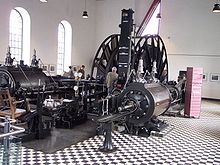

Steam winding engine of a coal mine from 1887, a horizontal two-cylinder compound engine with valve control, Nachtigall Colliery, Westphalian Industrial Museum
Questions and Answers
Q: What is a steam engine?
A: A steam engine is an engine that uses steam from boiling water to make it move. The steam pushes on the engine parts to make them move, and can be used to power many kinds of machines including vehicles and electric generators.
Q: When were steam engines first used?
A: Steam engines were first used in mine pumps starting in the early 1700s century, and were much improved by James Watt in the 1770s. They became very important during the industrial revolution where they replaced horses, windmills and watermills to work machines.
Q: How do steam engines work?
A: The first steam engines were piston engines. The steam pressure pushed on a piston which made it move along a cylinder and so they had a reciprocal (back-and-forth) motion. This could move a pump directly or work a crank to turn a wheel and work a machine. The heavy spinning flywheel smoothed out the power from the piston, while the governor controlled the speed of the engine.
Q: What powers a steam engine?
A: Steam to power a steam engine is made in a boiler that heats water to make steam. In most places fire heats the boiler, but fuel for this fire may be wood, coal, or petroleum; nuclear energy or solar energy may also be used instead of fire.
Q: How has technology changed since original types of piston engines?
A: During the 20th century pistons have been replaced by turbines which spin like windmill pushed by jets of steam, turning faster with more energy efficiency than original kinds of piston steams engines. These are now used in power plants to operate generators which make electricity as well as some ships being powered by these turbines too.
Q: What type of fuel can be used for boilers today?
A: Boilers for these modern turbines can be heated by many different types of fuel such as wood, coal, petroleum; nuclear energy or solar energy may also be used instead of fire depending on what is available at any given time