Plastic
Kunststoffe is a redirect to this article. For other meanings of both spellings, see Plastics (disambiguation).
Plastics (also plastics, rarely technopolymers, colloquially plastics) are materials that consist mainly of macromolecules.
Important characteristics of plastics are their technical properties, such as formability, hardness, elasticity, breaking strength, temperature resistance, heat resistance and chemical resistance, which can be varied within wide limits by the choice of macromolecules, manufacturing processes and, as a rule, by mixing in additives. Plastics are divided into three broad groups with respect to their physical properties: Thermoplastics, Thermosets and Elastomers.
Plastics are processed into moulded parts, semi-finished products, fibres or films. They are used as packaging materials, textile fibres, thermal insulation, pipes, floor coverings, components of paints, adhesives and cosmetics, in electrical engineering as material for insulation, printed circuit boards, housings, in vehicle construction as material for tyres, upholstery, dashboards, petrol tanks and much more.
The respective macromolecules of a plastic are polymers and are therefore made up of repeating basic units. The size of the macromolecules of a polymer varies from a few thousand to over one million basic units. For example, the polymer polypropylene (abbreviated PP) consists of multiple repeating propylene units. The polymers can be unbranched, branched or cross-linked molecules.
The polymers can be derived from natural substances or be purely synthetic. Synthetic polymers are produced by chain polymerization, polyaddition or polycondensation from monomers or prepolymers. Semi-synthetic plastics are produced by the modification of natural polymers (mainly cellulose to celluloid), while other bio-based plastics such as polylactic acid or polyhydroxybutyric acid are produced by the fermentation of sugar or starch.
Between 1950 and 2015, around 8.3 billion tonnes of plastic were produced worldwide - this equates to around 1 tonne per head of the world's population. Half of the production comes from the last 13 years. Of this amount, about 6.3 billion tons became waste, 9% of which was recycled, 12% incinerated, and 79% landfilled or accumulated in the environment. Plastics in general have been criticized because of the waste issue and possible health hazards.
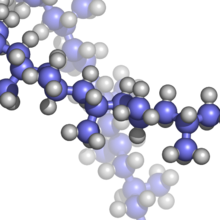

Polypropylene (sphere-rod model; blue: carbon; grey: hydrogen)
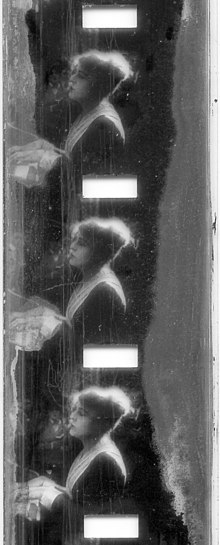

Celluloid - here an old film strip - is considered the first thermoplastic.
History of the development of plastics
Prepress
Biopolymers and naturally occurring polymers have been used by humans since time immemorial. All animals and plants contain polymers in their cells. Wood initially served humans as firewood and tools, for example as throwing wood, spears and as building material. The cell structure of animal skin or fur was stabilised by tanning, thus protecting it from rapid decay and making it into durable leather. Wool, cut animal hair, was spun and woven or felted to make clothing and blankets.
Birch trees provided the first plastic in the history of mankind, birch pitch obtained from birch bark by dry distillation, which was used by both Neanderthals and Stone Age Homo sapiens as an adhesive in the manufacture of tools.
In Mesopotamia, water basins and canals were sealed with natural asphalt. Likewise, certain tree resins were used there as gum arabic and exported to Europe. Amber is known from Europe as a fossil resin for use in arrowheads and jewelry. In the Middle Ages, animal horn was transformed into a plastically malleable material by certain process steps. As early as around 1530, transparent artificial horn was made from goat's cheese in the house of the Fuggers according to a recipe by the Bavarian Benedictine monk Wolfgang Seidel and sold.
Industrial history
Early developments
In the 17th and 18th centuries, naturalists brought elastic masses (rubber) obtained from milky tree sap from Malaysia and Brazil. The term rubber was introduced for these in Germany. Since the middle of the 19th century, a rapidly growing rubber industry developed.
In 1839, inventor Charles Goodyear discovered that rubber turns into rubber when heat is added to it. This process is called vulcanization. Charles Goodyear first manufactured rubber gloves from the new material. Around 1850 he also discovered hard rubber, a natural rubber hardened by heating in the presence of sulfur, which was initially marketed as ebonite. It was used, for example, to make jewellery, fountain pens, piano keys, tobacco pipes and parts of telephones. This first thermoset started the development of plastics as a material in the human environment.
The development of celluloid is due to several chemists. Christian Friedrich Schönbein developed gun cotton in 1846 by adding nitric acid to cotton. The Englishman Maynard dissolved gun cotton in an ethanol-ether mixture and obtained elastic skins (collodion) after evaporation. The Englishman Cuttin kneaded the collodion with alcoholic camphor solution to make celluloid. In 1869 John Wesley Hyatt used celluloid as a plastic and developed the first injection moulding machine three years later. Later, cellulose nitrate was developed in England for impregnating textiles.
Max Fremery and Johann Urban dissolved cellulose with an ammoniacal copper hydroxide solution. With this solution (cupro), copper-reeyon threads could easily be produced as the first viscose fiber.
Adolf von Baeyer described the polycondensation of phenol and formaldehyde in 1872. The Belgian chemist Leo Hendrik Baekeland investigated the effect of acid and alkali in this reaction and in 1907 developed a process (in technical production since 1909) for the production and further processing of a phenolic resin. This plastic, which he named Bakelite, was the first synthetic thermoset to be produced industrially in large quantities. Thanks to its suitability as an electrical insulator, it was used in the emerging electrical industry, among others.
Wilhelm Krische and Adolf Spittler developed galalith (artificial horn) in 1885. The synthetic material strongly resembles animal horn or ivory. The artificial horn is made from casein and formaldehyde solution. It was used, for example, to make buttons, pins, housings for radios, cigarette boxes, toys, and handles for umbrellas in a wide variety of colours.
The German chemist Fritz Hofmann applied for a patent on the synthetic rubber Buna in 1909. The first fully synthetic tires made of isoprene rubber were produced in 1912.
The Berlin pharmacist Eduard Simon described polystyrene in 1839. The styrene initially turned into a gelatinous mass. In 1909, Hans Stobbe studied the polymerization reaction of styrene in detail. It was not until twenty years later that this discovery was exploited.
In 1835, Victor Regnault discovered vinyl chloride, from which polyvinyl chloride (PVC) could be produced. The first patenting of PVC and of polymers made from vinyl acetate goes back to Fritz Klatte in 1912. However, Coroplast, which was one of the first companies to process PVC, is regarded as the worldwide pioneer in plastics processing. It was not until 1950 that this process was superseded by improvements from Dow Chemical.
As early as 1901, Otto Röhm was involved in the production of acrylic acid and acrylic acid esters, but it was not until 1928 that he found methacrylic acid methyl esters (MMA), which were more suitable for polymerization. The patent for polymethyl methacrylate (PMMA, brand name Plexiglas) granted in 1933 started a new era.
Development of polymer chemistry
Until the end of the 19th century, little was known about the exact structures of polymeric materials. It was only known from vapour pressure and osmosis measurements that they had to be very large molecules with a high molar mass. Mistakenly, the opinion existed that they were colloidal structures.
The German chemist Hermann Staudinger is considered the father of polymer chemistry. As early as 1917, he stated before the Swiss Chemical Society that "high-molecular compounds" consist of covalently bonded, long-chain molecules. In 1920 he published an article in the Reports of the German Chemical Society that is considered to be the foundation of modern polymer science. This was followed, especially in the years from 1924 to 1928, by further important theories on the structure of plastics, which form the basis for today's understanding of this class of materials. Staudinger received the Nobel Prize for this work in 1953.
Staudinger's work enabled the chemical industry to develop rapidly in the field of polymer chemistry on the basis of sound scientific principles.
The Munich chemist Ernst Richard Escales gave the materials group the name "Plastics" in 1910. The journal of the same name that he founded was first published in 1911.
Polyethylene was first produced under high pressure (200 bar) and at high temperatures in 1933 at Imperial Chemical Industries (ICI) in Great Britain. It was not until twenty years later that Karl Ziegler developed a process using catalysts made of aluminium alkylene and titanium tetrachloride that allowed ethene to be polymerised into polyethylene even at room temperature. The low-pressure polyethylene proved to be more heat-stable and mechanically more resilient. Shortly afterwards, Ziegler and Giulio Natta found a catalyst for the polymerization of propene to polypropylene. In 1955-1957, large-scale syntheses of polyethylene and polypropylene began. Today, the polyethylene (PE) and polypropylene (PP) produced in this way are, along with polystyrene (PS), the plastics most commonly used as packaging materials for food, cosmetics, etc. Ziegler and Natta were awarded the Nobel Prize in Chemistry in 1963 for their work.
Plastics made from polyesters were thought of very early (Berzelius, 1847). In 1901 there were glyptal resins (from glycerol and phthalic acid). Fritz Hofmann, Wallace Hume Carothers and Paul Schlack searched unsuccessfully for synthetic fibres based on polyesters. It was not until 1941 that the British Whinfield and Dickson succeeded in producing usable polyester fibres (polyethylene terephthalate, PET) at Calico Printers. Important polyester fibres were Dacron (DuPont), Diolen (ENKA gloss fabric), Terylene (ICI), Trevira (Hoechst).
In Ludwigshafen, the production of epoxy resins began in 1934 using a process developed by Paul Schlack. In 1935, the development of melamine resin was described simultaneously by Henkel (Mainkur) and Ciba (Switzerland).
In 1931, the US chemist Wallace Hume Carothers filed a patent with DuPont for a polyamide made from hexamethylene diamine and adipic acid. It was not until seven years later that the new synthetic fiber nylon (1938) was ready for sale. The caprolactam-based polyamide 6 produced by Paul Schlack in 1937 was christened Perlon. Industrial-scale production began in 1939 at IG-Farben. The production process of Perlon in Germany was cheaper than nylon production in the USA.
At about the same time, the Buna-Werke of I.G. Farben began producing Buna S and Buna N as synthetic rubber substitutes. In 1939 Otto Bayer developed polyurethane (PU) in Leverkusen.
At DuPont, the plastic polytetrafluoroethylene (Teflon) was developed by R.J. Plunkett in 1938. The product showed high temperature resistance and high chemical resistance. However, processing encountered problems. It was not until 1946 that Teflon went into large-scale production.
Silicone had already been produced from silanones by Frederic Stanley Kipping in 1901. It was not until 1944 that the synthesis of organosilicon halides with alkyl halides made it possible to produce silicone cheaply in the USA and Germany (Eugene G. Rochow, Richard Müller).
The polymerization of acrylonitrile had been known since the early 1930s. However, it was not usable as a plastic. The chemist Rein was able to dissolve polyacrylonitrile in dimethylformamide and thus make it usable for plastics production. In 1942, IG Farben developed a polymerization process for polyacrylonitrile. In 1942, Harry Coover (USA) discovered the "instant adhesive" methyl cyanoacrylate at Eastman Kodak.
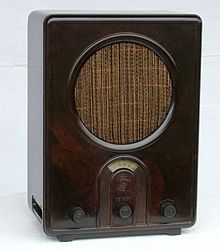

Volksempfänger with bakelite housing
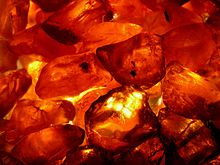

Natural "plastic" amber
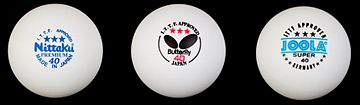

Celluloid table tennis balls
Division
Depending on the viewpoint of the observer and the requirements, plastics can be classified in different ways. Common classifications are mechanical-thermal behaviour (most common classification), origin (natural or synthetic), use or reaction of origin. A strict delimitation of individual plastics is often not possible, but these classifications provide a good overview.
Classification according to mechanical-thermal behaviour
The classification according to mechanical-thermal behaviour is made into thermoplastics, thermosets and elastomers. In addition, thermoplastic elastomers and reversible thermosets exist with a clearly subordinate importance. This classification is based on application technology. The different polymer classes differ in their mechanical properties due to the different cross-linking and the respective relationship between service temperature (usually room temperature) and physical transition temperature (glass transition temperature and melting point).
Thermosets consist of closely cross-linked polymers. Cross-links are shown as red dots in the figure. | Elastomers consist of wide-meshed cross-linked polymers. The wide mesh allows the material to stretch under tensile load. | Thermoplastics consist of uncrosslinked polymers, often with a semi-crystalline structure (shown in red). They have a glass transition temperature and are meltable. |
Thermoplastics
→ Main article: Thermoplastic
Thermoplastics are plastics that consist of long linear molecules. By adding energy, these materials become soft and malleable (plastic) any number of times and eventually melt. They can be formed into the desired shape by various primary and forming processes. After the workpiece has cooled, it retains its shape. This process is thus reversible (lat. reversible). The cause of this behavior is filamentary, linear macromolecules.
Most of the plastics used today fall into this group (polyethylene, polypropylene, polystyrene, polyester). They are used just as frequently for simple consumer goods, packaging, etc. as for technical parts in the automotive and electrical industries or in the construction industry, especially for roofing membranes, window profiles and pipes.
In order to create new, previously unavailable properties, two or more (mutually compatible) thermoplastics can be mixed (polymer blend).
Semi-crystalline thermoplastics (examples): POM - polyoxymethylene, PE - polyethylene, PP - polypropylene, PA - polyamide, PET - polyethylene terephthalate, PBT - polybutylene terephthalate.
Amorphous thermoplastics (examples): ABS - acrylonitrile-butadiene-styrene, PMMA - polymethyl methacrylate, PS - polystyrene, PVC - polyvinyl chloride, PC - polycarbonate, SAN - styrene-acrylonitrile copolymer, PPE - polyphenylene ether.
Thermosets
→ Main article: Thermosets
Thermosets (duromers) are polymers that are produced in a curing process from a melt or solution of the components by a crosslinking reaction. This irreversible reaction is usually caused by heating (hence the technical term thermosets), but can also be initiated and accelerated by oxidizing agents, high-energy radiation or the use of catalysts. Heating of thermosets does not lead to plastic deformability, but only to their decomposition. Cured thermosets are usually hard and brittle and can only be machined in the further manufacturing process. The reason for this behaviour are the spatially cross-linked macromolecules.
Because of their mechanical and chemical resistance even at elevated temperatures, they are often used for electrical installations. The most common and oldest type of plastic in this class is phenoplastics. This group also includes polyester resins, polyurethane resins for paints and surface coatings and virtually all synthetic resins such as epoxy resins.
Elastomers
→ Main article: Elastomers
Elastomers can change their shape briefly as a result of pressure or stretching; once the pressure or stretching has ceased, the elastomer quickly returns to its original shape. The elastomers are wide-meshed cross-linked and therefore flexible. They do not soften when heated and are not soluble in most solvents.
Elastomers include all types of crosslinked rubber. Cross-linking takes place, for example, through vulcanisation with sulphur, by means of peroxides, metal oxides or irradiation. 60 % of elastomers are used for tires. The remainder is distributed among other rubber articles, for example chemical gloves and hygiene articles.
Elastomers are natural rubber (NR), acrylonitrile butadiene rubber (NBR), styrene butadiene rubber (SBR), chloroprene rubber (CR), butadiene rubber (BR) and ethylene propylene diene rubber (EPDM).
Classification by origin
From a chemical point of view, plastics can be compared as macromolecular substances with other macromolecular substances. The various macromolecular substances can then be classified by origin into:
- natural macromolecular substances, such as hydrocarbons (rubber, balata), polysaccharides (cellulose, starch, pectin, chitin, cotton) and proteins (collagen, wool, silk)
- derivatives of natural macromolecular substances, such as cellulose nitrate, leather or gelatine
- synthetic macromolecular substances
- Derivatives of synthetic polymers (modification, for example, by saponification, introduction of reactive groups or subsequent cross-linking)
Only some of the macromolecular substances listed are plastics in the narrower sense, since plastics are defined as substances that are based on polymers and also undergo "plastic" states as materials during processing. Nevertheless, this classification can contribute to understanding.
Classification according to application
Depending on price, production volume and possible use, thermoplastics can be divided into the four application classes: Standard Plastics, Engineering Plastics, Functional Plastics and High Performance Plastics. Standard plastics (also: bulk plastics) are very versatile and are produced in large quantities. Standard plastics are often used as packaging materials and include, for example, polyethene or polyvinyl chloride. Engineering plastics have better mechanical properties than standard plastics and retain these properties above 100 °C and below 0 °C. Engineering plastics are often used for technical constructions and include, for example, polyethylene terephthalate and some aliphatic polyamides. Functional plastics serve a single function, such as acting as a barrier to flavors and gases in plastic packaging. Thermosets cannot be classified according to this scheme, but form their own class.
Compared to standard, technical and special plastics, high-performance plastics are characterised by their heat resistance and, in some cases, good mechanical properties. While the heat deflection temperature of standard plastics is usually only about 100 °C and that of engineering plastics reaches up to 150 °C, high-performance thermoplastics can withstand temperatures of up to 300 °C. High-performance plastics are quite expensive at around €20 per kg; their market share is only about 1 %.
The comparison of standard plastics, engineering plastics and high-performance plastics is illustrated by the following figure:
Classification according to reaction of origin
Plastics are produced by various polyreactions: polymerization, polycondensation and polyaddition. Accordingly, the product is called either polymerisate, polycondensate or polyadduct.
International abbreviation system
Individual plastics are designated according to a globally standardized abbreviation system, which for Germany is regulated in DIN EN ISO 1043 Part 1:2016-09: Basic polymers and their special properties, DIN ISO 1629:2015-03: Rubber and latices - Nomenclature (ISO 1629:2013) and DIN EN ISO 18064:2015-03: Thermoplastic elastomers - Nomenclature and abbreviations (ISO 18064:2014; German version EN ISO 18064:2014).
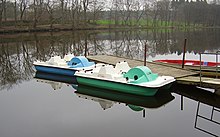

Pedal boats typically have a hull made of Duroplast
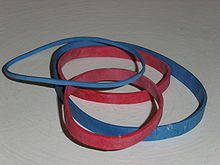

Elastic rubber band
Questions and Answers
Q: What is plastic?
A: Plastic is a material that can change its shape easily. Many things are made of plastic, and some types of wood can be made out of plastic, usually because making them in the right shape is easy and plastic gives form to wood and other things.
Q: Are all plastics man-made?
A: Most plastics are man-made; they do not occur in nature. The process of making plastics is usually quite complicated. Most of the materials that are called plastic are polymers. Polymers are long chains of atoms bonded to each other. In most plastics, the long chain is a chain of carbon atoms with other atoms attached to them.
Q: Who invented an early form of plastic?
A: Alexander Parkes, an English inventor (1813-1890), created an early form of plastic in 1855. It was hard but flexible and transparent. He called it "Parkesine" but now it is called "Celluloid."
Q: How does petroleum become part of the process for making plastics?
A: Plastics are mostly petrochemicals, made from natural gas or from petroleum, a type of oil. Chemical engineers refine the petroleum which goes through a heating process. It develops ethylene and propylene, which are the chemical building blocks for many plastics. These chemicals are then combined with other chemicals to produce a polymer.
Q: What kind of plastics can be used for 3D printing?
A: Some types of thermoplastic can be used for 3D printing because they will become soft enough when heated to form into different shapes, and then become hard again when they cool down.
Q: What happens to old plastics?
A: Old plastics are usually thrown away and put in landfills or recycled so they won't become waste.
Q: What materials may be added to some kinds of plastic?
A:Some plastics have other materials added to them like glass because this makes the plastic stronger and stiffer