Metal spinning
Spinning according to DIN 8584 (in practice also referred to as metal spinning or form spinning) is a manufacturing process of forming technology and, together with projecting and flow-forming, belongs to the group of spinning processes which is part of the tension-pressure forming. The spinning processes are used for the production of mostly rotationally symmetrical hollow bodies with almost any generatrix contour in small and medium quantities and are usually used in a combination of these processes.
Typical components that are manufactured by spinning are for example:
- Pots, cans and kettles for commercial kitchens
- Art and ornamental objects such as vases and goblets
- Parts of container and plant construction such as container bottoms or gas cylinders (dished bottoms, basket arch bottoms)
- Inlet rings and nozzles in aerospace technology
- Lampshades and reflectors
- Car rims
During spinning, a circular sheet blank (the so-called round blank) is clamped in front of the face of a spinning chuck. The spinning chuck represents the geometry of the component as an internal form (forming tool). The chuck is then rotated together with the blank by the main spindle drive of the spinning machine or, in individual cases, by muscle power.
The actual forming of the blank into the component is carried out in several stages by a spinning tool (universal tool), which is moved step by step from the centre of the blank to the edge and back again. As this movement progresses in the axial direction, the blank gradually approximates the geometry of the chuck. In industrial processes, the tool used is a spinning roller and the movement is computer controlled. In manual spinning part production, rod-shaped tools with differently shaped ends are often used. In this case, the tool is guided in a holder and moved by human hand movements. Theoretically, the sheet thickness of the original blank is retained during the forming process - due to the existing tension-compression stress condition. As the forming is only locally concentrated (in the partial forming zone) due to the geometry of the tools, only low forces are required, e.g. compared to deep drawing. Due to the locally limited forming, which only covers the entire component as time progresses, this is also referred to as an incremental forming process.
The good shape and dimensional accuracy of the components often makes machining unnecessary. As a rule, forming is carried out as cold forming (without additional heating from the outside). However, complicated components made of materials that are difficult to form also require intermediate annealing (heat treatment in the furnace) or hot forming, in which the blank is heated with a burner. Recent research also shows the possibility of carrying out the process with local, laser-assisted heating.
In addition to the forming of blanks, components that have already been preformed (e.g. deep-drawn or spun preforms) can also be further reduced in diameter by spinning. If this reduction in diameter only occurs locally on the component, it is referred to as drawing-in. Compressed gas cylinders, for example, are manufactured in this way. Conversely, large hollow bodies can also be expanded from the inside to the outside.
The process is very flexible and allows the forming of materials that are otherwise impossible or very difficult to form. However, the production of complicated components requires a great deal of experience and a high level of craftsmanship. Even today, the process is still strongly handcrafted and many components (lamps, ornamental objects, goblets, musical instruments, etc.) are still made by hand.
The term "printing" is derived from the former craft of metal working. The founder of the first trade union organisation of Austrian metal printers was Jakob Sokopp.
Currently, spinning processes are experiencing increasing industrial importance, especially in combination with flow-forming. With the production of internally toothed components, in which hubs are formed on in a single clamping operation, gear components can be produced economically that previously could only be manufactured by machining (clutch plate carriers, planetary gears).
The process was used, for example, at VEB Metalldrücker Halle.
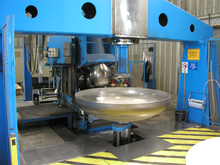

Large spinning machine


Pressing a dished end
See also
- Freeform
Questions and Answers
Q: What is metalspinning?
A: Metalspinning is a process where a piece of sheet metal is rotated on a machine (often a lathe) to produce an object.
Q: What kind of object is usually produced through metalspinning?
A: The object produced through metalspinning usually has the qualities of being round, hollow and symmetrical.
Q: How long has metalspinning been around?
A: Metalspinning has been around for thousands of years, dating back to Ancient Egypt.
Q: What is metalspinning closely related to?
A: Metalspinning is closely related to the potter's wheel.
Q: What is the process of metalspinning?
A: The process of metalspinning involves rotating a piece of sheet metal on a machine (often a lathe) to produce a round, hollow and symmetrical object.
Q: What are the qualities of the object produced through metalspinning?
A: The object produced through metalspinning usually has the qualities of being round, hollow and symmetrical.
Q: What historical period is associated with the origins of metalspinning?
A: The origins of metalspinning can be traced back to Ancient Egypt, which makes it an ancient technique.