Hydraulic fracturing
Hydraulic fracturing or fracking for short (also called "hydrofracking", "fraccing", fracing or frac jobs, also hydraulic fracturing, hydraulic fracturing, hydraulic fracture generation or hydraulic stimulation) is a method of creating, widening and stabilising fractures in the rock of a reservoir deep underground with the aim of increasing the permeability of the reservoir rock. This allows gases or fluids in them to flow more easily and steadily to the well and be extracted.
In fracking, a fluid (frac fluid) is injected through a well under high pressure, typically several hundred bar, into the geological horizon from which the well is to be extracted. The frac fluid is water, which is usually mixed with proppants, such as silica sand, and thickeners. Usually, several deflected boreholes (laterals) are first drilled in the target horizon by means of directional drilling, whereby the drill bit is guided parallel to the stratum. As a result, the available borehole length in the reservoir is considerably greater, which generally increases the production yield. High-volume hydrofracking uses large volumes of fluid with more than 1000 m³ per fracking phase or a total of more than 10,000 m³ per well.
Since the late 1940s, fracking has been used primarily in oil and gas production, as well as in tapping deep aquifers for water extraction and improving heat transport in deep geothermal energy. In the latter applications, no proppants or chemical additives are required. Since the beginning of the 1990s, and particularly in the USA from around the year 2000, extraction by means of fracking has focused on so-called unconventional crude oil and natural gas (including "shale gas"). The fracking boom there significantly changed the US energy market and caused prices to fall. This led to a debate about the viability of the process. Since around 2013, the US government has therefore been supporting efforts to increase the export of liquefied natural gas to Europe and Japan, among other things with accelerated approval procedures.
While some voices emphasize this geostrategic component by changing international dependencies, the environmental risks and possible health hazards of the "fracking boom" lead to a controversial and still ongoing technical, political and social debate, especially in Europe. Some countries and regions have legally banned natural gas fracking on their territory.

Fracking rig owned by Halliburton at the head of a well in the Bakken formation in the state of North Dakota
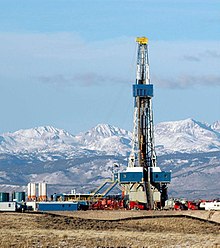

"Tight gas well in the Pinedale Anticline in the US state of Wyoming, with the Rocky Mountains in the background.
Application areas
In the first years after its development, the fracking method was mainly used to extend the production period of an oil or gas reservoir or to reduce the drop in the production rate in the late phase of the exploitation of a reservoir. These were so-called conventional reservoirs, with relatively high natural porosity and permeability of the reservoir rock.
Since the 1990s, however, fracking has increasingly been used to extract fossil hydrocarbons from so-called unconventional oil and gas reservoirs with low-porosity and impermeable reservoir rocks, whereby a distinction is made between primary and secondary reservoirs. In the case of secondary reservoirs, oil and gas have migrated from their source rock into a once sufficiently porous and permeable reservoir rock, the porosity and permeability of which has subsequently decreased significantly, so that today an insufficient production rate would be achieved if conventional production methods were used. This is also referred to as tight oil and tight gas.
More important is the application for production from primary deposits, where oil and gas are still in their source rocks. These can be either coal seams (CBM, Coal Bed Methane) or mudstones (shale gas, shale oil). Such mudstones are often petrographically incorrectly referred to as shales, which is partly traditional and partly due to an inaccurate translation of the English word shale ("thinly platy mudstone"). The gas and oil extracted from these mudstones is therefore called shale gas and shale oil respectively. In the case of shale oil, this can lead to confusion as to whether "mature" oil from primary deposits, i.e. "fracking oil", is meant or oil that has been extracted by processing from an "immature" oil shale.
"Fracking" is based on multiple horizontal wells within the reservoirs. Each well is fracked individually, with seismic monitoring to control crack propagation via the pressure level. The technique itself dates back to the 1940s, and was first used commercially in 1949. Other mining sectors have been fracking for longer. Since the significant increase in the price of oil and gas, fracking has become increasingly common, especially in the US (more than fifty thousand in 2008 alone). About 90 % of all gas wells in the USA are fracked, which created a temporary gas oversupply that led to the collapse of gas prices there.
Fracking is also used outside of oil and gas production to stimulate reservoirs, such as to stimulate water flow in deep geothermal energy, groundwater wells for drinking water supply and in mining for solid mineral resources. In some cases, wells are fracked for long-term pre-degassing of coal seams.
_Conventional_Deposits.svg.png)

Schematic representation of the production of crude oil and natural gas, left: conventional reservoir, right: unconventional reservoir.
Engineering
In hydraulic fracturing, a fluid (frac fluid), which may also contain a proppant, is injected into a well, usually several hundred to a maximum of about 3000 metres deep. The fluid pressure reached in the area to be fractured must exceed the lowest stress present in the rock and the tensile strength of the rock in order to fracture the rock. If this is the case, the fluid pushes the rock apart (tensile fracture). Normally, the horizontal components of the stress field are smaller than the vertical component because the vertical component - the lithostatic pressure resulting from the weight of the overlying rock layers - increases continuously with depth and is thus the largest of the principal stress components below a certain depth. Thus, tensile fractures caused by fracking occur predominantly as mostly near-vertical fracture surfaces that open in the direction of the smallest horizontal principal stress and thus propagate in the direction of the largest horizontal principal stress. On a smaller scale, the stress field can be oriented significantly differently, e.g. due to additional tectonic stresses.
After fracturing the formation, the injection pressure is reduced and most of the injected fluid, which is still under the pressure of the rock layer, flows back. This flowback water is called backflow or flowback. The added proppant remains in the fractures and keeps them open. Additives of the frac fluid also partly remain in the rock due to adhesion effects at the fluid-rock boundaries.
In order to optimally extract the dissolved gas, several wells are drilled from a drilling starting point, often almost horizontally in depth, but in any case within the target formation. The deviated wells are guided precisely in the reservoir using the so-called directional drilling method. The drilling path is controlled during drilling with the aid of a MWD (measurement while drilling) measuring unit placed directly behind the drill bit (geo-steering).
The deviated wells are then fracked individually and in sections, adapted to the geological and geomechanical subsurface conditions, several times (12 to 16 times). The aim of this "multi-well pad" process is to exploit the gas in the target horizon as spatially as possible from a larger volume of the well environment tapped by the fracs. It is this process that has enabled the breakthrough to large-scale industrial use of frac technology. In contrast, some shale gas fields in the United States and elsewhere, such as the Jonah gas field in Upper Green Valley, Wyoming, were previously developed using single vertical, non-frac wells. This required six to eight wells per square mile (equivalent to two to three wells per square kilometer). Today's technology drastically reduces the number of wells per square kilometer and especially the number of drilling sites, whereby the possible length of the deviated well sections in particular determines the drilling site grid. Today, drilling site distances of 10 km are quite conceivable.
Fracfluids
Fracfluids are fluids that are injected into the well and create artificial fractures in the gas-bearing target formation at high pressure. With the help of certain conditioned frac fluids, various proppants are introduced into the pathways created by fracking in order to stabilize them for as long as possible and guarantee gas continuity. A distinction is made between foam-based, gel-based and so-called slickwater fluids. The main component of the highly viscous, gel-based frac fluids is usually water tempered with additives, to which mainly tempered sand and ceramic beads (proppants) are also added. Gel-based frac fluids are mainly used in clastic rocks such as sandstones (conventional reservoirs).
In contrast, so-called extremely low-viscosity slickwater fluids are mainly used in claystones (unconventional deposits), which are made extremely flowable by adding friction reducers. Slickwater fluids consist of 98-99 % water plus 1-1.9 % proppants and less than 1 % additives.
The composition of the additives is normally named by the drilling and service companies to the regulatory authorities, but kept secret from the public. In Germany, the individual additives must be approved in accordance with the requirements of water law as part of the approval process for the wells.
Examples of possible additives and the purpose of their use are:
Additive | English designation | Realizations | Purpose |
Supporting means | Proppant | Quartz sand, sintered bauxite, ceramic beads, e.g. coated with epoxy or phenolic resin | Keeping open and stabilising the cracks created during fracking |
Gels, thickeners | Success Agent | Guar gum, cellulose polymers such as MC and carbohydrate derivatives | Increasing the viscosity of the frac fluid for better proppant transport |
Foaming agent | Foam | CO2 or N2 and foaming agents: tertiary alkyl amine ethoxylates, coco-betaines or α-olefin sulphonates. | Transport and deposition of the propping agent |
Deposition inhibitor | Scale inhibitor | Ammonium chloride, polyacrylates and phosphonates | Preventing the deposition and dissolution of poorly soluble mineral deposits in the borehole |
Corrosion inhibitor | corrosion inhibitor | Methanol, isopropanol, ammonium salts, sulphites, (e.g. amine bisulphite) | Protection of facilities, equipment and drill string |
Chain Breaker | Breaker | Sodium bromate, ammonium and sodium peroxodisulphate, enzymes | Reduction of the viscosity of gel-based frac fluids for better recovery of the fluids (destruction of the gel structure) |
Biocides | Biocide | terpenes, glutaraldehyde, isothiazolinones such as chloromethylisothiazolinone | Prevention of bacterial growth and biofilms, prevention of hydrogen sulphide formation (desulphurisation) |
Fluid Loss Additives | Fluid Loss Additives | Rinsing additives with thixotropic properties | Reduction of the outflow of the frac fluid into the surrounding rock |
Friction reducer | friction reducer | Latex polymers, polyacrylamide, hydrogenated light petroleum distillates | Reduction of friction within the fluids |
pH buffer | pH Control | Acetic acid, fumaric acid, potassium carbonate, borax, sodium acetate, sodium bicarbonate, sodium hydroxide | Buffer for adjusting the pH value |
Clay stabilizers | clay stabilizer | Potassium salts, e.g. potassium chloride, ammonium salts | Prevention and reduction of swelling of clay minerals |
Surfactants (wetting agents) | Surfactants | ethoxylated alkyl alcohols, nonylphenol ethoxylates | Reduction of the surface tension of the fluids to improve wettability |
Acids | Acids | Hydrochloric acid | Cleaning of the perforated sections of the drill string from cement and drilling fluid |
Hydrogen sulfide scavenger | H2S Scavenger | aromatic aldehydes | Removal of hydrogen sulphide (corrosion protection) |
Crosslinker | Crosslinker | triethanolamine, sodium tetraborate, citrus terpenes, zirconyl chloride, borates, organic zirconium complexes | Cross-linking of gel formers, increase of viscosity |
Solvent | Solvents | Ethylene glycol monobutyl ether, 1-propanol | |
Temperature stabilizer | temperature stabilizer | Sodium thiosulfate | Prevention of gel decomposition at great drilling depths |
Iron chelators | Iron Control | Citric acid, ethylenediaminetetraacetate | Prevention of precipitation of ferrous minerals in the target formation |
The composition of the frac fluids is determined separately for each well using decision matrices and/or computer programs and depends on the mineralogical-geological properties of the target horizon and the pressure and temperature conditions prevailing in the reservoir.
Clean fracking, on the other hand, refers to a new method of fracking in which only water, bauxite sand and starch are used.
Flowback and production water
Flowback water is the mud fluid that exits the surface of the wellbore during drilling and fracking until approximately 30 days later.
The water that is subsequently produced is composed of mud fluid, formation water (groundwater) and any dissolved gases and entrained solids therein and is referred to as production water. Approximately 20 to 50% of the frac fluid injected at depth is recovered as flowback water or with the production water and stored at the well site until disposal. The storage in open basins, which is common in some places in the American gas fields, cannot be approved in Germany. The containers in which the flowback or production water is stored are subject to water law requirements so that liquids are prevented from seeping into the ground.
The flowback and production water must be treated and processed in several stages before reuse or final disposal. First, the solids (cuttings) are separated at the well site in hydrocyclone plants, and the mud is disposed of. The recovered fluids, which are largely freed of solids, are usually transported by tanker trucks or through pipelines to a processing station. There, the oil phase, the remaining sludge and filtrate are separated in various tank farms with phase separators and filter systems. Depending on the hydrochemical properties, the residual water can either be mixed with fresh water and added back to the mud circuit or injected into approved injection wells in the margins of already developed or exploited hydrocarbon reservoirs. The light phase separated in these processes is further processed in refineries, and the filtrate is disposed of by certified companies.
In addition, various treatment methods, such as UV treatment, membrane filtration, coagulation and evaporation, are used to either reuse the frac fluids or reduce the amount to be disposed of.

Open pit with mud created from flowback water, near the well in the Bakken Formation, North Dakota. In Germany, such open pits would not be approvable.

Fracking well site in operating condition with feed lines

Mixing apparatus for mixing the frac fluids to the water, prior to injection into the well.
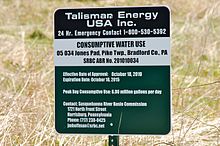

Sign indicating the regulatory approval of a domestic water withdrawal point in the northern Susquehanna River basin (Marcellus Shale Play, Pennsylvania, USA). The permitted maximum water withdrawal per day is listed as 6.0 million US gallons, about 23 million liters.