Formaldehyde
Formaldehyde (IPA: [ˈfɔɐ̯m.aldehyːt], , also [fɔʁm.aldeˈhyːt],
, systematic name methanal) is an organic chemical compound with the molecular formula CH2O and the simplest member of the aldehydes. Under standard conditions, formaldehyde is a gas with a pungent odour.
With around 21 million tonnes of annual production (as of 2019, based on 100 % formaldehyde), formaldehyde is one of the most widely produced organic chemicals. The technical production of formaldehyde takes place catalytically through the oxidation or dehydrogenation of methanol, for example in the silver catalyst process or the Formox process. In the chemical industry, it is used in particular as a starting material in the production of phenolic and urea resins. Another polymer is paraformaldehyde, which is used in cell biology, among other things. It is a powerful antiseptic and disinfectant available as a 40 percent solution of the aldehyde in water and is used as a fungicide and preservative.
In nature, formaldehyde occurs as an oxidation product of terpenes and as a metabolic product of bacteria that aerobically metabolize substrates with a carbon atom such as methanol, methane or methylamine to carbon dioxide. Formaldehyde is part of the human metabolism. It is classified as a carcinogen.
Nomenclature
The systematic IUPAC name methanal for molecular formaldehyde is derived from methane by adding the suffix -al for aldehydes. The preferred IUPAC name formaldehyde is derived from "formica", the Latin word for ant, since formaldehyde can be converted to formic acid by oxidation.
The aqueous solution of formaldehyde is called formalin or, more rarely, formol. It was marketed from 1893 as "Formalin" by Schering and as "Formol" by Hoechst. A saturated aqueous solution contains about 40% formaldehyde by volume or 37% by mass and is called "100% formalin". A stabilizer such as methanol is often added to this to suppress polymerization. A typical commercial formalin may contain up to 12% methanol. Production figures for formaldehyde are usually given on the basis of the 37% by mass formalin solution.
In aqueous solution, formaldehyde is present in its hydrated form as methanediol with the formula CH2(OH)2. Depending on concentration and temperature, this compound is in equilibrium with various oligomers called paraformaldehyde with a typical degree of polymerization of 8 to 100 units. Heating reverses the reaction and releases formaldehyde from paraformaldehyde. Solutions of formaldehyde in methanol (Methyl Formcel) containing 55.0% by mass of formaldehyde, 34.5% by mass of methanol and 10.5% by mass of water and solutions in butanol and isobutanol (Butyl Formcel) containing 40% by mass of formaldehyde, 53% by mass of butanol and 7% by mass of water are available under the trade name Formcel from Celanese. Trioxane is a trimer of molecular formaldehyde.
History
Alexander Mikhailovich Butlerov synthesized formaldehyde or paraformaldehyde in 1855 by reacting diiodomethane with silver acetate. He saponified the initially formed acetate by boiling it with water and concentrated the resulting solution in a vacuum. Butlerov, who named the resulting substance "dioxymethylene," did not realize, however, that he had produced paraformaldehyde. He investigated the chemistry of formaldehyde further and in 1861 discovered the formose reaction, in which a mixture of sugars is formed from formaldehyde.
Development of technical synthesis
In 1867, in search of the first member of the aldehyde series, August Wilhelm von Hofmann carried out the first specific preparation by dehydrogenating methanol on a glowing platinum wire. This laboratory procedure allowed the preparation of several liters of formaldehyde solution from methanol and thus further studies on the chemistry of this aldehyde. In 1872, for example, Adolf von Baeyer discovered its condensation with phenol to form phenol-formaldehyde resins, but without pursuing the discovery further.
Bernhard Tollens optimized the yield by regulating the ratio of methanol to air; to prevent explosions, he developed a flashback arrestor in the form of an asbestos structure, which he inserted between the methanol feed and the platinum spiral. Oskar Loew improved formaldehyde synthesis by using first iron(III) oxide and later copper as catalysts.
In 1888, the Mercklin & Lösekann company in Seelze began the commercial production of formaldehyde. From 1889 onwards, the demand for formaldehyde for dye production grew. Thus, acridine could be produced by reacting diphenylamine with formaldehyde under catalysis with zinc chloride. Acridine is the basic substance for acridine dyes such as acridine orange and acridine yellow, which until then had only been obtained from coal tar.
The company Meister, Lucius and Brüning, which took over a patent for the production of formaldehyde from Jean Joseph Auguste Trillat in 1890, had considerable interest in developing medical applications for aqueous formaldehyde solutions. In 1892, they commissioned the Frankfurt physician Ferdinand Blum to investigate the antiseptic properties of formaldehyde. Blum demonstrated the bacteriocidal properties of a 4 percent formaldehyde solution on bacteria such as Bacillus anthracis and Staphylococcus aureus. By chance, he discovered the possibility of fixing tissue samples with formaldehyde during his experiments.
Plastics from formaldehyde
The first major technical use of formaldehyde was the invention of galalith, a thermosetting plastic based on casein and formaldehyde, patented in 1897 by Adolf Spitteler and Wilhelm Krische. The plastic was successfully marketed and used for hair combs and accessories, knitting needles, pens, umbrella handles, white piano keys, electrical appliances and much more. In the German Empire in 1913, about 6% of the total milk production was used for the production of galalith.
Von Baeyer's work on the condensation of phenol and formaldehyde was taken up by various chemists, including Arthur Smith in 1899, A. Luft in 1902, F. Hensche in 1903, who investigated an alkali-catalyzed condensation, and H. Story in 1905. However, it was Leo Baekeland who realized the potential of this synthesis in 1907 with the production of Bakelite, the first fully synthetic plastic. His company, General Bakelite, began technical production of bakelite in 1910.
However, the bakelite products tended to darken and in the search for clearer plastics, the chemist Hans John discovered urea resins in 1918. The demand for urea and phenolic resins led to a sharp increase in the need for formaldehyde.
Large scale production
It was not until the development of methanol production from synthesis gas in a high-pressure process on zinc oxide-chromium oxide catalysts by Matthias Pier and Alwin Mittasch in the 1920s that the impetus was given for the development of large-scale production. Until then, the commercial production of methanol was only a by-product of charcoal production, which was started in Germany in 1857 by the company Dietze, Morano & Cie. in Lorch. In addition to charcoal and methanol, acetic acid and acetic acid methyl ester were produced as further products.
In the 1930s, Homer Burton Adkins, together with Wesley R. Peterson, developed the Adkins-Peterson reaction for the direct oxidation of methanol to formaldehyde. Adkins, who was working at the Bakelite Corporation at the time, used an iron-molybdenum oxide catalyst for this purpose. The annual production volume was about 25,000 tons in 1931 and had quadrupled to about 100,000 tons by 1943.
Use in the wood industry
In the 1940s, a plant in Bremen produced the first particleboard using urea-formaldehyde resins, triggering high demand in the construction and furniture industries. The processing of wood chips that this made possible increased the degree of utilization of trees from 40 % to 80 %.
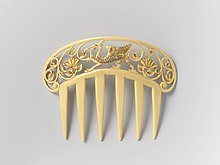

Galalith hair comb
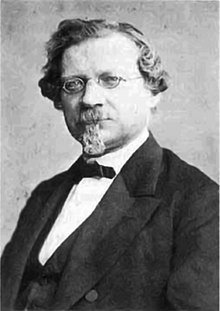

August Wilhelm von Hofmann, about 1871
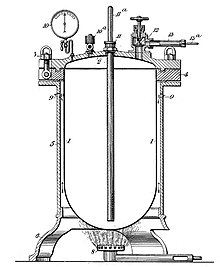

Apparatus for the preparation of formaldehyde according to J. J. A. Trillat