Fischer–Tropsch process
Fischer-Tropsch synthesis (also Fischer-Tropsch process, abbreviated FT synthesis) is a large-scale process for the production of hydrocarbons from synthesis gas, a mixture of carbon monoxide and hydrogen. The German chemists Franz Fischer and Hans Tropsch developed the process at the Kaiser Wilhelm Institute for Coal Research in Mülheim an der Ruhr and applied for a patent in 1925. The reactions take place in the presence of metal catalysts, temperatures of about 150 to 300 °C and pressures of up to about 25 bar. Contacts based on cobalt or iron serve as industrial catalysts.
In addition to coal, natural gas, crude oil or biomass are available as raw material sources for synthetic gas production. The products are liquid, low-sulphur synthetic fuels such as diesel fuel and synthetic engine oils. The longer-chain hydrocarbons produced, so-called paraffin slack wax, serves as a raw material base for the chemical industry or as Fischer-Tropsch wax as an additive in the adhesives industry, for coatings or in polymer processing. The by-products are oxygenated hydrocarbons such as ethanol and acetone as well as ethene, propene and higher olefins and alcohols. Co-products of the process are water and carbon dioxide. The product range of the Fischer-Tropsch synthesis can be controlled by reaction parameters, the type of reactor and the catalyst.
In the course of the National Socialist autarky policy, Fischer-Tropsch synthesis achieved great economic importance in Germany, as it helped to cover the demand for liquid fuels and lubricants and to provide chemical raw materials based on domestic coal. In South Africa, the Sasol company built large Fischer-Tropsch plants from the mid-1950s onwards to process synthesis gas from South African coal into motor gasoline and basic materials for the chemical industry. In Malaysia and Qatar, modern Fischer-Tropsch plants supply liquid fuels from natural gas.
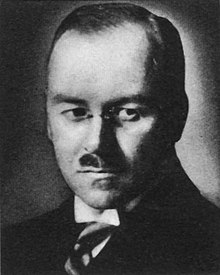

Hans Tropsch
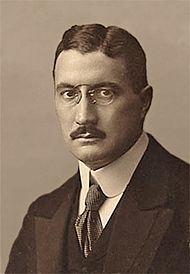

Franz Fischer (1911)
History
First work
The first work on the hydrogenation of carbon monoxide with hydrogen was carried out by Paul Sabatier and Jean Baptiste Senderens in 1902. Using nickel and cobalt catalysts, they obtained water and methane as the main products at atmospheric pressure and temperatures between 200 and 300 °C. The process would have increased the calorific value of town gas and avoided the toxic carbon monoxide it contained, but did not catch on due to cost. Sabatier received the Nobel Prize in Chemistry in 1912 for his work on hydrogenation.
In 1913, BASF filed a patent describing the production of saturated and unsaturated aliphatic hydrocarbons by hydrogenation of carbon monoxide at a pressure of about 100 bar and temperatures of 400 °C using nickel, cobalt, zinc and other metals or their oxides as catalysts.
Franz Fischer, founding director of the Kaiser Wilhelm Institute for Coal Research in Mülheim an der Ruhr, which was established in 1912 and whose maintenance was largely funded by the coal industry, focused his research in the early 1920s on the utilization of coke oven gas. This was a mixture of hydrogen, methane, nitrogen and carbon monoxide that was produced during the coking of coal and was available to heavy industry in surplus.
In 1921, together with Hans Tropsch, he developed a process based on alkalized iron-containing catalysts for the production of mixtures of oxygen-containing compounds from synthesis gas, the so-called synthol process. At a pressure of 100 to 150 bar and a temperature of about 400 °C, they obtained mixtures of aldehydes, ketones, carboxylic acid esters, alcohols and carboxylic acids, so-called synthol.
In the following year, the chemist Matthias Pier succeeded in producing methanol on an industrial scale by hydrogenating carbon monoxide in a high-pressure process on alkali-free zinc oxide-chromium oxide catalysts. Since the presence of iron led to methane formation, the reactors were lined with copper. The use of alkalized contacts yielded higher alcohols, especially isobutanol. With these successes, BASF focused its carbon monoxide hydrogenation research on methanol production and isobutyl oil synthesis.
Work at the Kaiser Wilhelm Institute for Coal Research
The shortage of petroleum and the associated bottleneck in fuel supplies during the First World War triggered a politically and militarily motivated search in the German Empire for alternative solutions, primarily based on domestic coal.
Fischer initially commissioned Otto Roelen, who had already been part of the Mülheim Institute since 1921 as Tropsch's assistant, to further investigate the synthol processS from 1924. After the oxygen-containing mixtures produced with it had proved unsuitable for use as motor fuel, Tropsch changed the reaction conditions and carried out the experiments under normal pressure. Although only low yields were achieved at the beginning, the work of Fischer, Tropsch and Roelen eventually led to the technical production of aliphatic hydrocarbons using cobalt or iron catalysts.
Large-scale process
During the Second World War, FT synthesis gained (wartime) economic importance in Germany. With it, the demand for liquid fuels, so-called Kogasin, as the synthesis product was called after its production sequence of coke, gas, gasoline, could be covered from domestic coal. By the end of the Second World War, the chemical industry had built a total of nine plants using FT synthesis, with a capacity of 0.6 million t/a.
Since Fischer-Tropsch fuels had a low octane rating, the National Socialist economic management built more hydrogenation plants instead, using the Bergius-Pier process, which provided a higher-grade motor gasoline; paraffin slack wax became difficult to obtain. It was not until 1940 that the Fischer-Tropsch plants significantly increased their output, resulting in a good supply of slack wax. At Imhausen's instigation, Wilhelm Keppler, the Commissioner for Economic Affairs, had the Fischer-Tropsch plants converted to the medium-pressure process, which provided a higher yield of paraffin slack wax.
A process developed by Arthur Imhausen used the higher molecular weight fraction, paraffin slack wax, for fatty acid synthesis by paraffin oxidation. The fatty acids were used as a raw material in the Märkische Seifenindustrie company, but from 1939 they were also used to produce a synthetic edible fat.
Production of synthetic fuel by the Fischer-Tropsch process | |||
Location | Operator | Input material | Production capacity |
Holten | Ruhrchemie | Hard coal | 60.000 |
Rauxel | Union Victor | Hard coal | 40.000 |
Wanne-Eickel | Krupp | Hard coal | 55.000 |
Bergkamen | Essen coal mines | Hard coal | 85.000 |
Dortmund | Hoesch | Hard coal | 55.000 |
Moers | Rheinpreussen | Hard coal | 75.000 |
Schwarzheide | BRABAG | Lignite | 180.000 |
Lützkendorf | Mitteldeutsche Treibstoff- und Oelwerke A.G. | Lignite | 30.000 |
Deschowitz | Schaffgotsch Petrol Ltd. | Lignite | 40.000 |
Total of all FT systems | 620.000 |
Postwar
FT synthesis products were never competitive with petroleum-based fuels, so the industry almost completely abandoned the process after the war. The plants were dismantled in accordance with the Washington Decision of the Western powers. After the oil crisis, however, research was resumed in the 1970s and a pilot plant was built in Bottrop. This was already shut down again at the end of the 1980s, as production was only profitable when the price of petrol was above 2.30 German marks.
Procedure of Sasol
In the Republic of South Africa, which also had sufficient coal resources and had to import crude oil, South Africa's first modern coal-to-liquid (CtL) plant was commissioned in 1955 for political reasons. It was built by the specially founded Suid Afrikaanse Steenkool en Olie (Sasol) with the participation of the German Lurgi AG. The pilot plant Sasol 1 was designed for about 6,000 barrels of fuel per day. From 1980 onwards, capacities were significantly expanded due to South Africa's political development.
Thus, in 1980 and 1982, Sasol commissioned Sasol II and Sasol III. This provided a total capacity of 104,000 barrels/day. With the political opening, the programme was extended to natural gas as a feedstock source, and in 1995 and 1998 Sasol created further capacity for 124,000 barrels/day of CtL and GtL (gas-to-liquid) fuel. Since hard coal can be extracted relatively cheaply from opencast mines, the country was still meeting about 40 % of its fuel needs from coal gasoline in 2006.
Sasol became the world market leader in XtL technologies through its South African developments and built a modern GtL plant in Qatar in 2006 with a capacity of 34,000 barrels/day. This is a high-temperature process with process temperatures of 350 °C (synthol and advanced synthol) that produces gasoline and alkenes as platform chemicals. Together with Foster Wheeler, Sasol also planned a Fischer-Tropsch plant in China. This plant, with an annual capacity of 60,000 barrels, uses a low-temperature process at 250 °C and is used to produce diesel fuel and waxes.
Raw materials turnaround
In 1993, the oil company Royal Dutch Shell commissioned its first GtL plant. The plant in Bintulu in Malaysia has a capacity of 12,000 barrels/day and is operated using a specially developed Fischer-Tropsch process, the Shell Middle Distillate Synthesis (SMDS process). Together, Shell and Sasol aim to build further GtL capacity of around 60,000 barrels GtL/day.
The USA has large coal seams lying close to the surface that can be relatively easily extracted by opencast mining. In view of rising fuel prices and simultaneously high demand, the United States Air Force tested a Boeing B-52H on 19 September 2006 at Edwards Air Force Base with a 50:50 mixture of ordinary JP-8 fuel and fuel derived synthetically from coal. The test flight was intended to clarify how this fuel would perform in practice and whether it could be reliably operated economically. An accompanying research project concluded that Fischer-Tropsch fuels offer an alternative source of JP-8 for the US Air Force.
In the course of the raw material turnaround, biofuels in particular moved into the focus of fuel production. In this context, Fischer-Tropsch synthesis received renewed interest from research and development. Although biomass-to-liquid fuels are being promoted as second-generation biofuels, especially in Europe, no BtL production has yet come on stream. Individual pilot projects have been initiated, and the now insolvent Choren Industries wanted to produce the BtL fuel they call SunFuel and SunDiesel at a plant in Freiberg, Saxony.
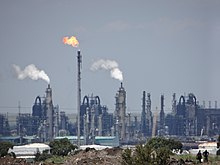

Sasol plants in Secunda, South Africa
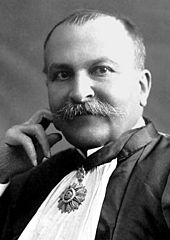

Paul Sabatier

Kaiser Wilhelm Institute for Coal Research, today Max Planck Institute for Coal Research
Proceedings
The capacity of Sasol's three coal-based Fischer-Tropsch plants in South Africa was approximately 7,500,000 tonnes per annum in 2001. The plants produce chemicals, linear olefins, motor gasoline, diesel and waxes. The capacity of the Mossgas plant in South Africa, which uses methane as feedstock, was approximately 1,020,000 tonnes per year in 2001. Typical products are motor gasoline and diesel. Other plants are in operation in Malaysia, Nigeria and Qatar.
The catalysts for industrial Fischer-Tropsch plants are based on cobalt or iron. Coal or other low-hydrogen raw materials are preferably produced with iron-based catalysts, as these simultaneously catalyze the water-gas shift reaction and thus help to provide the necessary hydrogen.
The provision of purified synthesis gas is usually the most complex sub-process of a Fischer-Tropsch plant. Its desired composition is in turn determined by the products to be produced. The composition in turn determines the choice of catalyst. The overall equation of the cobalt-catalyzed Fischer-Tropsch synthesis can be represented by the following reaction equation:
The iron-catalyzed reaction equation is:
Coal as a raw material
To provide the synthesis gas for Fischer-Tropsch synthesis, coal alone was originally first reacted with steam and air or oxygen to form synthesis gas at temperatures of over 1000 °C in coal gasification, for example in the Lurgi pressure gasifier, Winkler generator or Koppers-Totzek reactor. Since only a hydrogen-to-carbon monoxide ratio of 0.7 is achieved in the first step of this conversion, part of the carbon monoxide is reacted with water in a water gas shift reaction to form carbon dioxide and hydrogen until a ratio of 2:1 is achieved. The syngas is cooled, separating phenol and ammonia, and subjected to rectisol scrubbing, removing carbon dioxide, hydrogen sulfide, hydrogen cyanide and organics. The catalysts are sensitive to sulfur, and the hydrogen sulfide content is usually reduced to less than 30 ppb by volume. The clean gas still contains about 12 % methane, ethane, nitrogen and noble gases and about 86 % carbon monoxide and hydrogen in a ratio of 1:2.
Natural gas, biomass and waste as raw materials
The great advantage of the Fischer-Tropsch process is that any energy-rich raw material is basically suitable for the process. In addition to coal and natural gas, this also includes biogas, wood, agricultural waste or household refuse. The world's first plant for the use of solid biomass was built in 2005 in Choren near Freiberg. It went bankrupt in 2011.
In 2009, Fischer-Tropsch fuels (FT-SPK) received general approval by ASTM as aviation fuel. In 2014, airlines such as British Airways and Cathay Pacific preferred the production of FT fuels from household waste and had started to build corresponding plants in London and Hong Kong.
Pressure and temperature
The purified raw gas, which has a hydrogen to carbon monoxide ratio of about 2 to 2.2, is heterogeneously catalytically converted in a build-up reaction to hydrocarbons such as paraffins, olefins and alcohols. The end products are gasoline (synthetic gasoline), diesel, heating oil and raw materials for the chemical industry. The reaction already takes place at atmospheric pressure and at a temperature of 160 to 200 °C; technically, higher pressures and temperatures are used depending on the process. The synthesis proceeds according to the following reaction scheme:
(alkanes)
{alkenes}
{alcohols}
For every kilogram of fuel, about 1.25 kilograms of water are produced, for the production of which about half of the hydrogen used is used. Iron-containing catalysts catalyse the water-gas shift reaction, so that instead of water and the toxic carbon monoxide, carbon dioxide and hydrogen are produced:
Catalysts
A variety of catalysts are used in Fischer-Tropsch synthesis. The most commonly used are based on the transition metals cobalt, iron, nickel and ruthenium. Porous metal oxides with large specific surfaces such as diatomaceous earth, aluminium oxide, zeolites and titanium dioxide are used as supports.
The catalysts can be prepared by impregnating the porous metal oxides with metal salt solutions and subsequent calcination. The catalyst activity is increased by promoters, these are not themselves catalytically active catalyst components, such as alkali metals or copper. Furthermore, the pore size distribution of the support, the calcination and reduction conditions and by the resulting particle sizes of the active catalyst metal influence the catalytic activity. Substances such as alkali metals, which are good promoters for iron catalysts, act as catalyst poisons in cobalt catalysts, for example. Cobalt, nickel and ruthenium remain in the metallic state during the reaction, while iron forms a series of oxides and carbides. However, it is suspected that cobalt oxides, which remain due to incomplete reduction of the salt used, have a promoter role.
Catalysts containing iron and cobalt are usually obtained by precipitation, often together with other metals and other promoters. The original catalyst of Fischer and Tropsch was prepared by co-precipitation of cobalt, thorium and magnesium nitrate, with the diatomaceous earth added to the freshly precipitated catalyst. The further steps such as shaping, drying and reduction of the cobalt salt significantly affect the activity of the catalyst. Cobalt catalysts show only low activity in the water gas shift reaction, while iron catalysts catalyze it.
Procedure
The process management is determined by the need to remove the large reaction heat of about 3000 kilojoules per cubic meter of converted synthesis gas. The temperature is removed by water, the temperature of which is controlled by adjusting the pressure. Excessively high temperatures lead to methane formation as well as rapid coking of the catalyst.
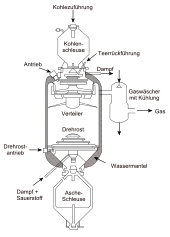

Schematic of the Lurgi pressure carburetor