Vitreous enamel
This article is about the enamel coating. For electronic mail, see email.
The enamel ([eˈmaɪ̯] or [eˈmaːj]; South German, Austrian: [eˈmaɪ̯l]) or (more commonly) enamel ([eˈmaljə], [eˈmaɪ̯] or [eˈmaːj]; from French émail, from Old Frankish *smalt, cognate with schmelzen; also found as fused glass or smelting) refers to a mass of inorganic composition, usually consisting of silicates and oxides, produced by melting, fritting, or sintering (meaning a melting process stopped short of melting together) in usually vitreous solidified form. This mass, sometimes with additives, is usually applied in one or more layers to a support material and melted at high temperatures and for short firing times, usually aiming to coat the support material. Enamel is used on metal or glass as a substrate.
Glass flux is also used as a synonym for enamel (however, glass flux is also the collective term for glasses produced with metal inclusions, such as gold flux, blue flux, green flux and purple flux for jewellery production).
The specification for "enamel" published by the RAL Institute is used to distinguish similar products in the trade. RAL-RG 529 A3 contains the valid "definitions for enamel(le)". All techniques and materials not corresponding to this definition, such as ceramic glazes, are not designated as "enamel". However, word combinations such as "enamel varnish" or "enamelling paste" are permissible. However, these materials have nothing to do with enamel in the sense of this article. In addition to the technical-legal definitions of the RAL Institute, it should be noted with regard to the linguistic usage of enamel: The technical language of art history and handicrafts prefers the term enamel, which is used to designate both material and technique as well as a (small) enamelled object or an enamelled part.
Cold enamel, on the other hand, is a synthetic resin mixed with color pigments that solidifies without heating and is used to make jewelry.
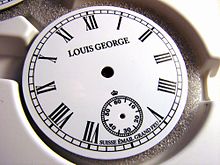

Wristwatch enameled tin dial

Historical information sign in the DB Museum Nuremberg
History
The protective function of enamel on everyday utensils is an innovation of the 19th century. Older enamel works have a decorative character throughout. The first known enamel work is 3500 years old and was found as grave goods in Mycenaean tombs on Cyprus. The ancient Egyptians also knew enamel work, both on gold and on iron. The Celts reached a further high point in enamel technology in 500 BC with blood enamel.
In the Middle Ages, enamel was used in the art of goldsmithing. The first flowering of enamel art occurred around the year 1000 (cellular enamel, cloisonné), possibly promoted by the Empress Theophanu, who came from Byzantium (compare the cover of the Codex aureus Epternacensis).
Delicate flexible gold strips were soldered onto a metal plate in such a way that they formed the outline of the desired figure. The resulting cells (cloisons) were filled with different coloured enamel powders and heated until the mass melted. This was repeated until the required height of enamel was reached. A central workshop for this technique was probably located in Trier. An important example of this art is the Pala d'Oro in Venice. Even in the early period, translucent glass flows were often used, which allowed the golden metal background to shine through.
The Meuse region emerged in the 11th century with works using the pit enamel process (émail champlevé), whose heyday was in the 12th century in the Cologne area. Here, opaque enamel colours were preferred, the surfaces of which were no longer separated by bars, but filled depressions that were dug out of the metal with a burin. Later, blue work from Limoges (Limosin enamel) gained in importance until the 13th century and was widespread throughout much of Europe. In the 14th century, translucent enamel, now applied to silver grounds gridded in relief, returned. In small plates the design, usually figural, was engraved or cut so as to form a very flat but sharply defined relief, and then the whole surface was covered with transparent enamel of different colours. Where the layer became thinner, the silver shone through and gave the bright spots, while shadows prevailed on the thicker layers. This resulted in an extremely delicate effect of the enamel work.
A typical type of enamel work for the early modern period is painter's enamel, which originated in Limoges in the 16th century. Here, the coloured areas are no longer separated by bars or metal parts, but colours applied with a brush and merging into one another enable miniature-like, fine, pictorial representations. In order to avoid distortion of the support material (and thus cracks in the enamel), the reverse side of the main representation was also covered with enamel (contreémail [contre-émail]), which could also be decorated. Important artists are Pierre Reymond, Jean Courtais and Léonard Limousin. In the 17th century this technique was replaced by enamel painting. In this technique, only the metal oxides were painted onto the white enamel ground and fired on. The technique was used especially in France and Switzerland, but also in Germany. Watch covers and tobacco boxes were typical applications of this decorative art. After the decline of enamel art in the middle of the 18th century, it was not until a century later that a revival in the field of ecclesiastical goldsmithing brought a revival of the old enamel art. This revived the medieval techniques, and in the later 19th century one also remembered the decorative possibilities of the Renaissance and imitated (not infrequently with the intention of forgery) the models of the 16th century. Important sites were Aachen, Cologne, Vienna, Mechelen, Brussels, Lyon and Paris. In the 20th century, in the spirit of contemporary trends (Expressionism, New Objectivity), enamel art was also revived in the Werkkunstschulen.
Stimulated by demand, the Japanese, Chinese and Indians also began to take up and perfect the art of enameling again.
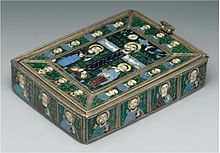

Reliquary, Metropolitan Museum of Art
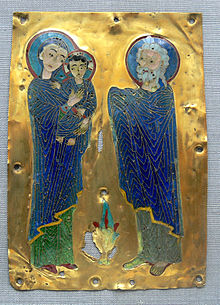

Presentation of Christ, Byzantine, gold cell enamel; 12th century Kunstgewerbemuseum Berlin, Inv.-Nr. 27,19
Composition
From a chemical point of view, enamel is a melting mixture. The glass-forming oxides are silicon dioxide (SiO2), boron trioxide (B2O3), sodium oxide (Na2O), potassium oxide (K2O) and aluminium oxide (Al2O3). The oxides of titanium, zirconium and molybdenum serve as opacifiers. To ensure that enamel adheres firmly to metallic substrates, it also contains cobalt or nickel oxide. The ceramic pigments most commonly used are iron oxide pigments, chromium oxides and spinels.
Questions and Answers
Q: What is enamel?
A: Enamel is a coating made of melted glass, often used on metal, glass, or ceramics.
Q: How is enamel made?
A: Enamel is made by fusing powdered glass to a base through firing at temperatures usually between 750 and 850°C (1,380 and 1,560°F).
Q: What are some other names for enamel?
A: Enamel is sometimes called vitreous or porcelain enamel.
Q: How long has enamel been used for decorative purposes?
A: Enamel has been used for decorative objects for two or three thousand years, especially in the Middle Ages in Europe.
Q: When was enamel used on everyday objects such as kitchen equipment and road signs?
A: Enamel was used on everyday objects such as kitchen equipment and road signs in the 19th century.
Q: What are some advantages of enamel?
A: Enamel is hard-wearing, scratch-resistant, and easy to clean.
Q: What is enamel typically used for?
A: Enamel is typically used as a coating on metal, glass, or ceramics for decorative or functional purposes.