Electroplating
Electroplating is a redirect to this article. See also: Electroplating (pressing plant).
Electroplating refers to the electrochemical deposition of metallic deposits, i.e. coatings on substrates (workpieces) in an electrolytic bath.
In electroplating, electric current (direct current) is passed through an electrolytic bath. At the positive pole (anode) there is usually a metal such as copper or nickel, which is dissolved and transferred to the negative pole (cathode). The metal ions dissolved in the electrolytic bath are deposited by reduction on a workpiece which is electrically connected to the negative pole and thus serves as the cathode. Alternatively, the metal ions may already be present in the electrolyte as a solution. The metal ions are deposited relatively uniformly on the workpiece at the negative pole and the layer thickness increases over time. Often a pre-treatment of the substrate is necessary before the galvanic process.
Electroplating is the most common application of electroforming technology. This coating process is used to produce metallic coatings on substrates.
The second area of electroforming is galvanoplastics (also electroforming). Larger layer thicknesses allow solid metallic bodies to be created. The process was used from the 19th century onwards to produce artistic sculptures and casting moulds. Today it is used in mould making for injection moulding of plastics and more recently in microsystems technology as micro electroforming, see Lithographic Electroforming (LIGA).
On the one hand, galvano refers to a printing process in which the wooden printing block is replaced by a galvanically produced facsimile printing forme. On the other hand, galvano also refers to the copy of a coin or medal, as well as occasionally sculptures, which were produced by galvanic means.
The application of low-frequency ("galvanic") current in medical galvanotherapy is also misleadingly referred to as electroplating.
.svg.png)

Galvanic copper plating of a metal (Me) in a copper sulphate bath
History
The history of electroplating, as it is colloquially known, goes back to the Italian physician Luigi Galvani (1737-1798), who discovered galvanism, named after him, at the end of the 18th century when, during experiments with frogs' legs, he noticed that they twitched when touched with two electrodes made of different interconnected metals.
Alessandro Volta realized that the effect was caused by the various metals. These, in combination with an electrolyte, produce an electrical voltage that discharges in the animal muscle. He then built his battery, the voltaic column, which played an important role in the foundation of electrical engineering. It was probably the first battery ever made, although there is speculation that humans built batteries thousands of years ago: Certain clay vessels found near Baghdad, in which a copper cylinder with an iron rod was embedded, have been interpreted as the first batteries. The electrolyte used is unknown. They are dated to about 2000 BC and are usually referred to as the "Baghdad battery". Today, however, it is doubted that it was really a battery. Accordingly, it is also questionable whether electroplating was already possible in ancient times. The assumption that the gilding of objects with the help of electroplating techniques was known in antiquity is therefore not proven.
The first documented galvanic gilding took place in 1805 by a student of Volta. In 1840, the English entrepreneur George Richards Elkington received a patent for a process for galvanic silvering with cyanide-containing solutions. He used the process in the company he founded with his cousin. It employed nearly a thousand workers in 1865, when Elkington died, and was considered the leading electroplating company at the time. From the middle of the 19th century, life-size statues such as equestrian statues were produced by electroplating, for example the famous statue of the Great Elector in Berlin, which was based on designs by Andreas Schlüter.
The relatively non-toxic application of metallic coatings has largely replaced the technique of fire gilding or silvering, which is harmful to health due to the mercury used in this process.
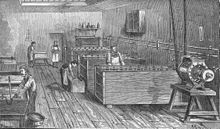

Historic electroplating shop, around 1900

The voltaic column enabled the first experiments in electroplating.
Galvanic applications
A distinction is sometimes made between decorative and functional electroplating. The former is mainly used to embellish objects and must have certain minimum technical properties for this purpose. Examples of decorative electroplating are plastic electroplating, the chrome plating of tubular steel furniture, fittings and motorcycles, and the gold plating of jewellery and cutlery.
Functional electroplating is used for corrosion protection, wear protection, catalysis, improvement of electrical conductivity and reduction of friction forces. The ductility and formability of workpieces can also be improved by electrodeposited coatings. The following are some examples:
- Galvanizing of screws (corrosion protection)
- Coating of machine parts with hard chrome (wear protection)
- Coating with metallic catalysts, mostly containing nickel or platinum, for the chemical industry or fuel cells (catalysis)
- Gold and silver plating of electrical contacts (electrical conductivity)
- Lead-tin-copper coatings for plain bearings (friction reduction)
- Copper plating during wire drawing (improvement of formability)
Due to their wear resistance and good sliding properties, hard chrome coatings can also be used as coatings for hydraulic cylinders or for immersion tubes in suspension forks. The end properties of these components after coating are considerably better than those of their base materials, for example.