Computer-aided design
This article deals with computer-aided design. For other meanings, see CAD (disambiguation).
CAD (from computer-aided design [kɔmˈpjuːtɐ ˈeɪdɪd dɪˈzaɪn]) refers to the support of design tasks by means of EDP for the manufacture of a product (e.g. car, aircraft, building, clothing).
Which activities fall under the term CAD is treated differently in the literature. In a narrower sense, CAD is understood to mean the computer-aided creation and modification of the geometric model. In a broader sense, it is understood to include all computer-aided activities in a design process, including geometric modeling, calculation, simulation and other information acquisition and information provision, from concept development to transfer to production or manufacturing (work preparation).
While CAD applications were initially used primarily for the production of manufacturing documents (marketing term: CAD as computer aided drafting/draughting), with increasing computer performance CAD systems with complex expert systems and integrated FEM solutions became available for the design and construction of technical solutions, whereby the objects are treated as three-dimensional bodies from the outset (three-dimensional CAD). Any necessary technical drawings can be automatically produced from the virtual models of three-dimensional objects. A particular advantage of 3D CAD is the ability to create an image of the objects from any direction. The 3D printer enables the transition from the virtual model to the real object, which is also used in the hobby sector. Together with the material properties that can be captured, extended CAD models are created to describe the physical properties (for example, strength, elasticity) of the objects.
CAD is part of the so-called CAx technologies, which also include computer-aided manufacturing (CAM) or computer-aided quality (CAQ). CAD is used in almost all branches of technology: architecture, civil engineering, mechanical engineering, electrical engineering and all their disciplines and mutual combinations up to dental technology.
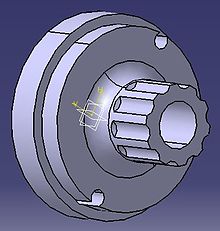

A virtual part in a view from any direction (3D CAD program CATIA)
Use of the CAD
CAD is used to generate digital design models of various types, which provide the information from which the desired product can be manufactured (via technical drawing, NC transfer, etc.). The advantage of the computer-internal representation of the model is the rationalization of the construction process. The functionalities of CAD aim, for example, to relieve the designer of routine tasks (for example, through the versatile use of the 3D or feature model or through the automatic hatching or dimensioning of technical drawings) or to be able to change models easily and quickly even in advanced phases of the design process (for example, by means of parametrics) or to prevent loss of information and errors. The generated CAD models can be used in a variety of other applications (e.g. in simulation or calculation processes or as a digital mock-up), and the results from these applications in turn modify the CAD model, whereby the design is continuously optimized (and thus the product quality increased) until the product is ready for production.
In the area of virtual product development, CAD, as part of CAx technologies, supports, from a more technical point of view, in particular the creation of process chains (CAD-CAM), integrated modeling (for example by means of features), the continuous flow of information on the basis of a uniform database (digital master), the modeling of complete product models (virtual product) and, from a more organizational point of view, the faster provision of information (for example via parametrics and 3D modeling), in particular in the early phases of the development process (frontloading) through distributed and parallel working methods (simultaneous/concurrent engineering).
Another area of application is the modeling of manufacturing processes with CAD software. This enables a cost-effective and comparatively quick insight without semi-finished product consumption and machine assignment to the manufacturing process used.
CAD modeling tools
CAD uses various tools that originate in different areas, such as in particular geometric modeling (which in turn draws on, for example, differential geometry, set theory, matrix algebra, graph theory) or theoretical and applied computer science (for example, software engineering, data structures). These tools can be combined and vary depending on the CAD system and industry. In some cases, they are not an integral part of a CAD system, but can be installed as an (industry-specific) extension (add-on, plug-in), whereby the database for the model remains the same.
CAD systems are vector-oriented (opposite: raster-oriented), because this way all geometric objects can be traced back to lines and points and can be completely characterized.
2D modeling
In 2D modeling, geometric elements are drawn in a plane, mainly in the form of sections and views of components. The working method is similar to that of a manual drawing. You select the desired command (for example, "Draw line"), select the necessary points for modeling the object in the model environment and the program creates the desired object. In particular, lines (straight lines, distances), free-form curves (splines), circles/circular arcs and points are used, which can be assigned further attributes such as line thickness, line type (for example, dashed, dash-dotted, dotted) or color.
Furthermore, different transformations (translation, scaling, rotation, mirroring, shearing, etc.) can be applied to these geometric objects or equidistants (offset curve) can be derived from them. They can also be trimmed or chamfered as closed polylines, rounded or filled with a color or pattern. Texts, symbols or external image files (e.g. scanned hand sketches that serve as templates) can also be inserted into the model environment.
2D modeling is mainly used for the generation of volumes, which were created from two-dimensional geometry elements by certain operations from the 3D area (extrusion, sweeping, rotation, etc.). Furthermore, 2D modeling is used in those areas where a 2D model is sufficient for the representation and explanation of a component, or where 3D modeling would be too costly in relation to the benefits, or also as a supplement to technical drawings that were generated from a 3D model. Furthermore, it is used for drawing graphics of technical details of a component or for mere schematic representations of constructions (e.g. for explaining concepts, considerations, instructions for production).
3D modeling
→ Main article: Geometric modeling
In 3D modeling, geometric objects are built up and stored in a three-dimensional form. Thus, on the one hand, they allow a realistic representation and better spatial perception of the body during and after modeling, on the other hand, certain representation-related (for example, representation of sectional and view representations from different angles), document-related (technical drawings, parts lists, work plans, spare parts catalogs, assembly and operating instructions) and technical-visual representations (collision consideration, explosion representations, assembly, installation, assembly examinations) can be (partially) automated by the system due to the three-dimensionality. Furthermore, the 3D description of an object is a prerequisite for many other applications in and outside the CAD system (DMU, MBS, CFD, FEM, NC machining, virtual reality, rendering, 3D printing, etc.) and thus supports the creation of process chains (especially CAD-CAM process chain) in virtual product development. However, this advantage of the wider range of applications of 3D models is offset by a higher design effort, a correspondingly extensive knowledge and practice with the modeling tools.
The 3D models can be transformed (translation, scaling, rotation, etc.) or deformed (tapering, twisting, shearing, buckling) by means of various spatial operations, similar to 2D.
The following internal computer representation types occur in CAD:
Edge models
In the edge model (also wire-frame model), an object is represented only by its edges, without volume or surface information. This means that no geometric operations are possible that require a surface or a volume as a prerequisite (for example, penetrations require a volume for the automatic creation of the penetration edges). Therefore, pure edge models are only used in very specific cases, for example, as a basis for the creation of surfaces or volumes or as auxiliary geometry. If you still want to have a 3D model as an edge model for display reasons, you model a surface or solid model and merely change the (graphical) display type.
Surface models
Surface models are described exclusively in terms of their surfaces, as the "shell" of a body (without information as to whether a point lies on the inside or outside) and are always used where surfaces of a product are to have a complex shape (such as car bodies, aircraft fuselages, consumer goods), which cannot be achieved by means of mere solid modelling and an intuitive modification of the surface is desired. Both analytically describable surfaces (translation surfaces, ruled surfaces) and analytically non-describable surfaces (e.g. B-spline, Nurbs surfaces) are used, whereby almost any conceivable shape can be generated in high geometric quality (Class A surface) with respect to surface transition (continuity), surface degree, number of surface segments. There are a wide variety of generation options. For example, surfaces can be created from boundary curves, via a "movement" (e.g. lofting, sweeping) from several planes or spatial curves or lines, or via a curve network (skinning), or they can be created as a "blending surface" of two surfaces. If required, the freeform surface can then be deformed by manipulating the support points via a "control mesh" stretched over it, which results from the degree of the surface and the number of support points. Analysis tools such as the colored representation of the Gaussian surface curvature, the display of curvature combs or the representation by means of isophotes help to check the continuity and smoothness of the surface. Subsequently, it is possible to convert closed surface composites into a solid. Furthermore, surface models are used for the approximation to a polygon mesh, which originates from a point cloud, which a 3D measuring instrument (e.g. a tactile or optical system or CT method) has created from a real object (in the course of reverse engineering).
Volume models
In solid modeling, geometric objects are stored as solid bodies (and not just as shells, as in surface modeling). It describes the geometry and, if a material density is specified, the mass of a body ("body model") unambiguously and completely, which is why the objects can be interpreted automatically by the system and the geometric consistency remains assured when the object is manipulated. Due to this, it has the highest degree of automation, which is why various operations, such as the determination of certain properties of the body such as moments of inertia, center of gravity, weight can be performed automatically by the system. Solid modelers can draw on an extensive pool of modeling echics. Thus
· volumes can be created over 2D drawings using various transformations (for example, extrusion, rotation).
· volumes can be changed or globally deformed by Boolean operations or by trimming with planes.
· Primitives (for example, cuboids, spheres) can be manipulated using subdivision surface techniques.
· closed surface composites are transformed into solids.
· solids can be created from system-internal (for example, cuboid, sphere, cone), company-specific or standardized (for example, standard parts) templates.
In CAD, there are mainly 2 ways in which solids can be represented internally in the system:
Constructive Solid Geometry
In CSG modeling, a model is constructed from primitives (e.g. cuboids, cylinders) by means of set-theoretic operations and stored internally in the system as a path and not as a final product. The advantage of CSG-modeling lies in the always consistent description, because already the basic elements are consistent and the recognizability of the history of origin. This is offset by the disadvantage that elements such as edges and surfaces are not directly addressable and therefore cannot be manipulated.
boundary representation
With the B-rep the volumes are determined hierarchically downward from the boundary surfaces over the boundary edges, whereby here the determination of the consistency (by means of Euler operators) must always be checked. The advantage of this volume presentation is that edges and surfaces can be addressed directly and thus manipulated. A history of origin does not exist.
Since the advantages and disadvantages of the representation types can be balanced against each other, "hybrid modelers" are predominantly used in CAD.
Direct modeling
In explicit modeling, the geometric elements are changed directly using specific functions (scaling, moving, stretching, etc.). The geometric elements contain only fixed values (and no variables), which can only be changed by applying functions. The geometric element and the corresponding function that is to cause the desired change are selected and the object is changed either interactively with the mouse or by entering coordinates using the keyboard. Only the selected geometric elements are changed. In contrast to parametric modeling, there are no permanent dependencies between the geometric elements, which makes it possible to change the geometry very intuitively and freely.
Due to this very free modeling possibility, direct modeling is mainly used in the early concept phase, where a fast and uncomplicated change of the geometry (without understanding the "creation chronology" of the parametric model or searching for the "right" parameter that causes the desired change) is desirable. Furthermore, direct modeling can be helpful when changing imported ("foreign"), parameterized CAD models due to, for example, unclear or incomprehensible chronology or due to file format transfer errors. The model is adjusted by selecting and then dragging, moving or similar the desired surfaces or edges and the change is planted in the chronology tree (for example, Synchronous Technology in NX or Live Shape in CATIA).
Parametric modeling
Parametric modeling means controlling the model by means of parameters. This means that - in contrast to direct modeling - the model is not addressed directly via its geometry, but via its parameters, which can change the model at any time. Depending on the application, the types of parameters roughly differ into geometry parameters (for example geometric dimensions, positions), physical parameters (for example materials, loads), topology parameters, process parameters (for example tolerances, data for heat treatments or NC travels). Because these parameters are stored internally in the system, relationships and dependencies can be established between them. This is implemented via restrictions or constraints. Here, the values entered or automatically linked from an external program (e.g. spreadsheet program) are "held", whereby their dependencies and relationships can be calculated (using mathematical calculation methods) (constraint-based design). These restrictions can be, for example, dimensions, algebraic relations (length = 2 × width), logical operations (if length > 5 cm, then width = 8 cm, otherwise 12 cm) ("explicit restrictions") or also the horizontality, parallelism or congruence ("implicit restrictions") of geometric elements. This makes it possible to build an intelligent model that can be controlled with "knowledge" in the form of design rules and only a few decisive values ("knowledge-based parametrics").
In the two-dimensional domain, parametric modeling is performed using dimensions and restriction displays that represent the parameters and are associatively linked to the geometry (dimension-driven geometry). The user first starts to draw the geometry roughly. The system tries to recognize the design intent (by means of rule-based methods) by applying implicit restrictions, which are indicated by a restriction display in pictogram form. Subsequently, the user can individually attach dimensions (with the values) to the geometry until the geometry is completely defined by parameters. The geometry can now only be changed via the parameters.
Parametric modeling can also be used to insert standard parts or even entire assemblies from a library into the model environment, while maintaining the changeability of the underlying parameters.
Due to the manifold relationships and dependencies in parametric modeling, a design methodology has evolved that requires the user or designer to ensure clean, error-free parameterization and a logical structure of the CAD models in its geometric design.
Chronology-based modeling
Data structures are used here that record the creation process of the model. For the user, this is displayed in a chronology tree (history tree), which is continuously updated during the modeling process and in which the individual modeling steps and the structure of the model can be viewed and, if necessary, changed in each phase of the design process.
In this way, certain dependencies ("parent-child relationships") are shown in the chronology, which indicate the generation path of the model, such as the 2D drawing ("sketch") underlying an extrusion or the solid body underlying a penetration. The respective elements are linked associatively, i.e. if the underlying element (e.g. the 2D drawing) changes, the element based on it (e.g. the solid created from the extrusion) automatically changes as well.
Assembly modeling
In assembly modeling, separately stored CAD models ("individual parts") are assembled into a holistic model ("assembly") by referencing, whereby the file created in this way only contains references to the models and no geometry. Here, the individual parts can be related to each other (for example, by means of distances to surfaces or points). An assembly structure tree facilitates the overview.
The advantage of assembly modeling is especially the overall representation of the product with its individual parts and serves to check collisions and assembly (packaging) or visual inspections (for example, "fly-through analysis") or kinematics analysis.
feature-based modelling
Feature-based modeling is the use of features for design purposes in the model environment. In CAD, features represent tools with which design aspects can be implemented as a unit in the model and manipulated (using parametrics). They have a higher information content (for example, on technological, manufacturing or quality-related aspects) that goes beyond pure geometry and can be accessed by other applications (for example, CAM, FEM, CAPP), which leads to a higher degree of automation of the processes and makes features "information and integration objects" in the entire product development process.
The features can be of a geometric (shape features) and/or semantic nature, can combine a variety of product information and therefore exhibit considerable flexibility and variety in the type and scope of their representation, which is why they can also be used in all industries. Examples of this are bores with additional tolerance information in mechanical engineering or multi-layered wall constructions with all material characteristics in architecture. However, this high degree of flexibility also brings with it the disadvantage of the difficult transfer or conversion of features from one program to another. The categorization of features (feature taxonomy), the transfer of individual features by means of certain "mapping techniques" (feature mapping) or the storage of the feature from different constructional or manufacturing perspectives as an integrated model (multiple-view feature modeling) can help here, but are currently still the subject of research.
Features can be created in 3 different ways. Due to the connection between features and parametrics, all features can be changed afterwards via their parameters.
- Interactive feature recognition: In this process, a feature model is generated from a geometry model by the user interactively selecting the respective geometric elements to be defined as features one after the other. The user is either completely free to select the geometric elements or is supported by the CAD system through a feature library with predefined features. The system then generates the desired feature and displays it in the chronology tree.
- Automatic feature recognition: In this process, a geometry model is translated into a feature model by the CAD system automatically deriving the corresponding features from the respective geometry using algorithms.
- Design by features: In this method, features are created from generic templates from a (native or company-specific) feature library. The user simply selects the desired feature, enters the parameter values, and inserts it into the model environment. The created feature can then be connected to other features (for example, fillet) or modified using parameters. With this type of generation, the user is bound to the predefined, generic features, so it is possible to create user-defined features in the CAD programs. The advantage of this method is that the designer can insert information from the beginning, which can be used for downstream processes and thus one works with a continuously high level of information in the product development process. The disadvantage is a relatively large feature library with predefined features.
Macro Technology
The macro technique is used in CAD to create frequently used geometry or features with only a few inputs, whereby the macro is resolved after the objects have been created. It is therefore no longer possible to determine afterwards whether an object was created via macro. A distinction is made between two types:
- Shape macros: Shape macros are predefined, permanently stored (i.e. without stored variables) geometric elements (for example, washbasins, chairs in architecture or screws in mechanical engineering) that are selected from a macro library and inserted as a whole into the model environment. The geometric element created in this way can then be broken down into its individual components again if required (using commands such as "Explosion") and processed using direct or parametric modeling (by "reparameterizing").
- Command macros: Command macros are summarized stored commands, which are executed one after the other with only one command input and generate the corresponding geometry in the model environment. They can either be entered individually by the user or the CAD system records the individual design steps in the form of command sequences in a file ("log file", "program file"), which the user can access and modify and optimize according to his wishes. The transition to variant programming is smooth.
Variant programming
In variant programming, the model is generated using native or higher level programming languages such as C++, Python, Fortran, or scripting languages such as Visual Basic for Applications, or AutoLISP. The user writes (optionally with utility support) the desired modeling steps in a text editor to generate the model. The CAD system reads and executes the procedures and creates the result in the model environment. If you want to change the model, the corresponding changes are generally made in the text (and not in the model environment), and the model is then recalculated and changed by the system. However, the model can also be planted in the model environment as a discrete model (i.e. equipped with fixed values) and changed by means of direct modeling or parametric modeling (by "reparameterizing"). Furthermore, some systems offer "visual programming languages" (for example Rhino 3D in combination with Grasshopper) with which geometric models, algorithmic and parameterized, can be created without programming knowledge.
General aids
CAD systems also have other capabilities that support the user during modeling. An essential element of CAD systems is the viewport, in which the model is displayed pictorially. It is possible to view the model in different projection modes (e.g. axonometric, perspective) and from different distances (zoom), to pan or rotate it. The user can work in only one viewport or in several viewports simultaneously. The object can be modeled in each of the viewports, but they can be controlled separately in terms of projection type or graphical representation (for example, a shaded representation in one viewport and a wireframe representation in another). It is also possible to display 3D sectional representations of the geometry or model sections in a view frame with simultaneous suppression of the geometry outside the view frame (clipping).
In order to be able to move and position geometric objects in space more easily, various aids are used, such as coordinate systems (for example, Cartesian or polar coordinate systems on the one hand and world and working coordinate systems on the other), object snaps (with which, for example, end points, circle centers or tangent points of already existing geometries can be recognized and snapped onto), alignment at temporary "track lines" at certain angular intervals or at a predefined grid.
Furthermore, there are some techniques for organizing the model. One of them is the layer technique. Different objects, such as dimensions, constructive objects, texts, etc. can be categorized in order to keep the model clear and to be able to show/hide the objects later if necessary (for example, because they were only auxiliary geometries) or to give them the same attributes (such as the same line type or color) or to lock/unlock them so that they cannot be changed or selected during the modeling process. Another way of organizing is to combine objects into a group in order to be able to perform the same operations, such as transformations, for all objects contained in the group.
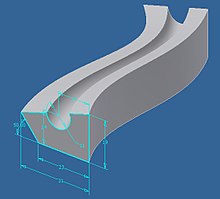

Example of a volume generation over a planar, parametric 2D drawing along an arbitrary curve ("sweep")
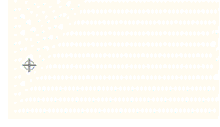

Example of the creation and machining of a free-form surface
Questions and Answers
Q: What is computer-aided design (CAD)?
A: Computer-aided design is the use of computer software to assist in creating, altering, analyzing, or optimizing designs.
Q: What are the benefits of using CAD?
A: CAD helps create better quality, more precise, and neater designs, improves communication of the design by creating documentation and a database for manufacturing.
Q: In which fields is CAD commonly used?
A: CAD is commonly used in architecture and product design.
Q: Does designing using CAD take longer than the traditional way of drawing on paper?
A: Yes, designing using CAD can take longer than the traditional way of drawing on paper.
Q: Why does designing using CAD cost more?
A: Designing using CAD costs more due to the cost of the software.
Q: Do people need to be trained to understand CAD?
A: Yes, people often need to be trained to understand CAD.
Q: What is the purpose of creating documentation and a database for manufacturing using CAD?
A: The purpose of creating documentation and a database for manufacturing using CAD is to improve communication and make manufacturing more efficient.