Carbon fibers
This article presents fibers made of carbon. For the composite material made from them, see Carbon fiber reinforced plastic.
Carbon fibers - also known as carbon fibers or carbon fibers - are industrially manufactured fibers made of carbon-containing raw materials that are converted into graphite-like carbon by chemical reactions adapted to the raw material. A distinction is made between isotropic and anisotropic types: Isotropic fibers have only low strengths and less technical importance, anisotropic fibers show high strengths and stiffnesses with simultaneously low elongation at break in axial direction.
The most important property of carbon fibers as a stiffening component for lightweight construction is the Young's modulus; the Young's modulus values of the best fibers are close to the theoretical Young's modulus of graphite in the a-direction.
A carbon fiber or filament has a diameter of about 5-9 micrometers. Usually, 1,000 to 24,000 filaments are combined to form a multifilament yarn (roving), which is wound up. Further processing into textile semi-finished products such as woven fabrics, braids or multiaxial fabrics is carried out on weaving machines, braiding machines or multiaxial knitting machines or, in the production of fibre-reinforced plastics, directly on prepreg plants, strand drawing plants (pultrusion plants) or winding machines.
As short cut fibers, they can be blended with polymers and processed into plastic components via extruder and injection molding systems. In addition to these low-filament types, there are also so-called HT types with 120,000 to 400,000 individual fibers, which are mainly processed into short-cut fibers, but also into textile fabrics. It is also possible to produce such heavy tows with subtows, e.g. in the form of seven times 60,000 individual filaments.
The fibers are mainly used for the production of carbon fiber reinforced plastic (CFRP = C-fiber reinforced plastic). The abbreviation CFRP (Carbon Fiber Reinforced Plastic) is also used.
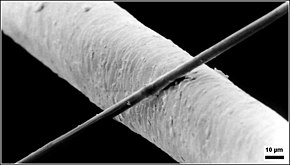

6 µm thick carbon fiber compared to a 50 µm thick human hair.
Properties
Typical properties of HT carbon fibres | |
Density | 1.8 g/cm³ |
Filament diameter | 6 µm |
Tensile strength | 3530 MPa (N/mm²) |
Train-E-Module | 230 GPa |
Elongation at break | 1,5 % |
Typical properties of UMS carbon fibres | |
Density | 1.8 g/cm³ |
Filament diameter | 6 µm |
Tensile strength | 4560 MPa (N/mm²) |
Train-E-Module | 395 GPa |
Elongation at break | 1,1 % |
Electronegativity (EN) χ | 2,50 |
Carbon fibers are electrically and thermally very good conductors, the electronegativity EN has a very high value of 2.50. The difference to iron (EN=1.64) is very high at 0.86, which is already considerably corrosive in the presence of an electrolyte. In comparison, the difference between iron and aluminium (EN=1.47) is only 0.17. Carbon fibres also have a negative coefficient of thermal expansion in the longitudinal direction at lower temperatures. When heated, they therefore initially become shorter and thicker.
From the two aforementioned properties, there is a compelling need to insulate carbon fibre-based components from other metallic components, both mechanically and electrically, if temperature fluctuations and contact with outside air, water and, in particular, seawater as well as other electrolytes (for example melt water with road salt in road traffic) are to be expected in the case of use. The advance of electrocorrosion of iron, which is in direct contact with carbon fibres, is high under a suitable electrolyte.
- Specific heat capacity: 710 J/(kg-K)
- Thermal conductivity: 17 W/(m-K)
- Coefficient of thermal expansion: −0,1·10−6/K
- Specific electrical resistance: 1.6-10-5 Ohm-m (= 16 Ω - mm2/m)
Carbon fiber types:
- HT - High Tenacity
- UHT - very high strength (Ultra High Tenacity)
- LM - Low Modulus
- IM - intermediate (Intermediate Modulus)
- HM - high stiffness (High Modulus)
- UM - (Ultra Modulus)
- UHM - (Ultra High Modulus)
- UMS - (Ultra Modulus Strength)
- HMS - high stiffness/high strength (High Modulus / High Strain)
According to this list, the spectrum of properties is broad: the available tensile strengths range from about 3500 MPa to 7000 MPa, the tensile stiffnesses from 230 GPa to almost 600 GPa, and the elongations at break are in some cases less than 1 % at high stiffnesses, while they can be as high as 2 % at low stiffnesses combined with higher strengths.
Manufacture
Thomas Alva Edison received a patent as early as 1881 for the carbon-fibre incandescent lamp he developed with filaments made of pyrolysed bamboo fibres.
A major step was taken in 1963 with the production of fibres with directional crystal structures at the Royal Aircraft Establishment in England.
Carbon fibers are produced from organic starting materials. Compounds that can first be converted into an infusible intermediate stage and then carbonized to form carbon in a pyrolysis process while retaining their shape are primarily suitable. By stretching (applying a tensile stress) during this temperature treatment step, the orientation of the atomic structure in the fibers can be changed in such a way that higher strengths and stiffnesses of the fibers are achieved during carbonization.
During this carbonization treatment, all elements except the main carbon component are split off in gaseous form. The relative carbon content increases with increasing temperature, which is usually in the range of 1300 to 1500 °C. This results in a carbon content of 96 to 98 percent by weight.
One speaks of graphitization above 1800 °C. Here, above all, the structure of the graphitic carbon layers is more and more perfected. However, the layer plane spacing between these carbon layers remains above the value known from the actual graphite. For this reason, the term "graphite fiber (fibre)", which is commonly used in English, is not strictly speaking correct. This also applies to the terms "graphite fiber" and "carbon fiber" used in German-speaking countries.
The annealing treatment increases the modulus of elasticity due to the structural approximation to the graphite lattice, but the strength is reduced as a result.
The structural diversity of the fibers with the wide range of properties results from the anisotropy of the graphitic layers, which can be controlled via the manufacturing parameters. In the case of continuous fibres, depending on the fibre type, almost the theoretical stiffness value is achieved, but usually only 2-4 % of the theoretical strength. In the case of fibers that are deposited from the gas phase in a manner deviating from the method described above (so-called whiskers with a very short length), significantly higher strengths can be achieved.
Today, there are three established starting materials for continuous carbon fibers:
Rayon/Viscose (Cellulose)
The cellulose-based viscose fibers produced via the viscose process are the starting material for the carbon fibers here. Due to the starting material, these do not have a perfect carbon structure. They thus have a comparatively low thermal and electrical conductivity. (In their use as filaments, however, their high ohmic resistance was favourable). They are therefore mainly used as insulating materials with high thermal resistance (in the absence of air/oxygen), for example in furnace construction.
Polyacrylonitrile (PAN)
Most of the high-performance fibers (HT/IM) in use today are manufactured from polyacrylonitrile by stabilization reactions in air and subsequent pyrolysis under inert gas. Their essential characteristic is their high tensile strength. A distinction is made between low filament and multifilament yarns (HeavyTow). The latter use the cheaper production technologies of the textile industry, which is why they are the most cost-effective.
Pitch (of different origins)
Pitch is much cheaper than PAN as a raw material, but the cleaning and preparation costs are so high that fibres made from PAN are still cheaper.
If the pitch is merely melted, spun and carbonized, isotropic carbon fibers with lower strength values are obtained. Only the transfer into the so-called mesophase by means of a hydrogenation treatment allows an orientation of the carbon network planes along the fiber axis by stretching during the manufacturing process.
This then also allows the production of fibers with high stiffness (HM). With simultaneous high tensile strength (HMS), these fibers are only used in special applications for cost reasons.
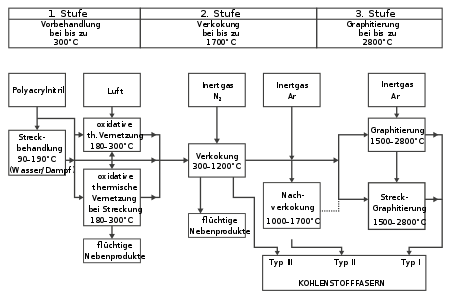

Manufacturing process based on polyacrylonitrile: Type III: IM fibre and Type II: HT fibreType I: HM fibre