Airbus A400M Atlas
The Airbus A400M Atlas is a military transport aircraft manufactured by Airbus Defence and Space. The A400M is increasingly replacing or supplementing the largely obsolete inventory of Transall C-160 and Lockheed C-130 Hercules tactical transport aircraft in the air forces of seven European NATO nations. Compared to these, it is distinguished by its higher payload, transport volume, speed and range, thus enhancing European capabilities in the field of strategic airlift. Like its predecessors, the four-engine shoulder-wing aircraft is equipped with turboprop engines and a drivable tail ramp, and can operate from short, unpaved runways as well as airdrop paratroopers and loads. The intended range of operations also includes uses as a hospital and tanker aircraft. The new development of the EPI TP400-D6 engines required for the project was carried out by the Europrop International consortium of companies founded specifically for this purpose.
The contract, concluded in 2003 between the procurement organisation OCCAR and Airbus after decades of preliminary planning, covered the development, production and initial support of 180 aircraft at a fixed price of 20 billion euros. The first delivery was scheduled for October 2009. The customers are Belgium, France, Germany, Luxembourg, Spain, Turkey and the United Kingdom. Malaysia was added as an additional customer in 2005. After several delays, the first flight took place on December 11, 2009. Airbus managed to renegotiate the contract, whereupon in 2010 the customer states assumed part of the billions of euros in additional costs, cancelled some aircraft and accepted a later delivery. The unit price thus climbed from 125 million euros to 175 million euros.
On 1 August 2013, the French armed forces took delivery of the first aircraft in series production. The first operational mission, a flight to Mali, took place at the end of December 2013. After Turkey and the United Kingdom, the German Air Force became the fourth customer to receive its first aircraft in December 2014, followed by Malaysia in March 2015 and Spain in November 2016. The 50th aircraft was delivered in summer 2017.
While the aircraft type is in operational service in several air forces, the development of promised partial capabilities and overall delivery has been further delayed. The final version is expected in 2021, more than eleven years behind schedule. Aircraft already delivered are to be retrofitted by 2027, unless individual capabilities that prove too difficult to implement are actually dropped. Users complain of low operational readiness and quality deficiencies in initial flight operations. The project will burden Airbus Group's finances with provisions of more than 8.8 billion euros.
Development
Requirements
The A400M is designed to meet increased military airlift requirements. As a tactical and strategic transporter, the Airbus A400M is intended to provide European armed forces with the ability to react quickly and move large quantities of material and personnel in the event of intra- and extra-European crises arising, thanks to its high range, speed and cargo capacity, spacious cargo hold and flexible deployment options. In addition to purely military tasks, the aircraft is to be available for the evacuation and rescue of nationals and humanitarian aid missions (see also Petersberg tasks). Compared to the types the A400M replaces, payload and range are approximately doubled. The possibility of air-to-air refuelling further increases the range; with a conversion kit, the transporter itself becomes a tanker aircraft. It is designed to carry loads up to the size of an armoured personnel carrier or medium helicopter. The tactical capabilities of the predecessor models are to be largely retained or improved. These include low-level flight, autonomous operations without ground crew, ground facilities and ground-based landing aids, short take-off and landing capability on unprepared sites, steep descent and all-weather operations. Paratroopers should be able to be dropped and loads loaded and unloaded via a tail ramp without other aids or dropped in flight from high altitude or near the ground.
Beginnings
In the early 1980s, recognizing the need to replace the gradually aging inventory of transport aircraft such as the Lockheed C-130 Hercules and Transall C-160 in European countries, Aérospatiale, British Aerospace, Lockheed and Messerschmitt-Bölkow-Blohm (MBB) formed the Future International Military/Civil Airlifter consortium (FIMA) in December 1982 to study the feasibility of a joint military transport aircraft. In 1985, the defense ministers of the Independent European Programme Group unified the requirements for the aircraft, clearing the way for international cooperation on the project. Three years later, an Outline Staff Target for the new aircraft was available. In the meantime, Aeritalia and CASA had joined FIMA in 1987; two years later Lockheed dropped out of the project. In 1991, the EuroFlag consortium was formed in Rome by the companies to develop and build the aircraft. At the same time, the Prefeasibility and later Feasibility Phase was started, which was to investigate the feasibility of the development goals in relation to customer requirements. In September 1994, a 1:1 model of the A400M was on display at the Farnborough Airshow under the name Future Large Aircraft (FLA). A year later, the EuroFlag consortium disbanded again, with the project now being continued by Airbus.
In 1996, the European Staff Requirement (ESR), which had since been amended and was the subject of constant debate, was updated. In September 1997, seven states submitted a request for proposals and in December of the same year decided in principle in favour of the aircraft, now called the A400M, although binding commitments were not forthcoming. The decision in favor of a European indigenous development was controversial. In Germany, Defence Minister Volker Rühe favoured the idea of cooperation between Antonov and Airbus with the aim of further developing the Ukrainian Antonov An-70 transport aircraft, which already existed as a prototype, rather than entrusting Airbus alone with the construction of a new "Future Large Aircraft". Airbus rejected the AN-70 as the basis for the FLA project in 1998. In addition, the acquisition of the American Lockheed C-130J and Boeing C-17 types was investigated. Based on the request for proposal and the ISR, Airbus Military Company (AMC) submitted a bid in January 1999. The offer included fixed services at fixed prices and dates (commercial approach).
The European deficits that became apparent in 1998/1999 during the intervention in the Kosovo war, which led to dependence on the USA even for intra-European operations, underscored the need for the long-planned aircraft.
Since 2000
On 16 May 2000, UK Defence Secretary Geoff Hoon announced the intention to purchase 25 A400Ms for the Royal Air Force. On 9 June 2000, about a month before Airbus parent company EADS went public, the political decision of the two main customers in favour of Airbus was announced in Mainz. It was made during the 75th Franco-German summit between President Jacques Chirac and Chancellor Gerhard Schröder. Germany stated an operational requirement of around 75 aircraft and France of 50. The focus was on the further development of the European Security and Defence Policy and the formation of a coherent and common European air transport fleet. The summit declaration included the wish for the industry involved to seek opportunities for cooperation with Russia and Ukraine. In addition, as the development of the Airbus A380 was pending and the establishment of a European satellite-based reconnaissance network (SAR-Lupe/Helios) was decided, French Prime Minister Lionel Jospin spoke of Europe's ability to "embark on great industrial adventures".
In June 2001, the armaments agency OCCAR was designated as the contractor for the project, and a contract for the delivery of 196 aircraft was signed in Brussels on 18 December 2001. However, it did not come into force because the German Bundestag refused to finance the 73 aircraft earmarked for the Bundeswehr. It was only after a reduction of the German share to 60 that the final contract for now 180 aircraft at a price of 20 billion euros was signed in Bonn on May 27, 2003. In the same month, the engine of a European consortium (see propulsion) was selected for the aircraft - instead of an offer from Pratt & Whitney Canada. On 26 June 2008, the transporter was officially presented at EADS in Seville.
Construction of the first prototype began at the end of 2007. The A400M was scheduled to enter series production in 2008. The rollout of the first aircraft on the final assembly line in Seville took place on 26 June 2008, and the first ground tests began on 3 September 2009. According to Airbus, the first flight of an Airbus A400M was planned for late summer or autumn 2008; the first delivery, originally scheduled for October 2009, was initially postponed by six months - with the risk of a delay of a further six months. France was due to receive its first A400M in spring 2010; it was to be delivered to the Bundeswehr in 2011. Since the old Hercules and Transall aircraft cannot remain in service for that long, an interim solution was sought on various occasions. The German Air Force decided to charter six Antonov An-124-100s through the SALIS program, which had been developed in the meantime. Lockheed Martin also made a lease offer for four Hercules C-130Js.
On 22 April 2008 in Seville, Carlos Suarez, in charge of the Airbus military division, announced that internal costs for the project had increased by 1.4 billion euros. He also confirmed that Airbus was still having problems with the A400M's engines. The approval of the digital monitoring and control software (FADEC) of the engines according to civil standards alone led to a delay of more than one year with the corresponding increase in costs.
Airbus announced further delays due to engine problems together with a cost increase of another 314 million euros on 24 November 2008. Program manager Tom Williams also announced that the first flight would take place towards the end of 2009.
On 10 January 2009, the Financial Times Deutschland (FTD) published an article according to which the Airbus Group was "facing a complete revision of the 20 billion euro fixed-price order for 180 aircraft". The reason given was that at the moment neither the planned dead weight of the aircraft nor the targeted payload could be achieved. It is now assumed that delivery will take place in 2013. In detail, there were problems with the engine software (which, according to MTU Aero Engines, was three times as complex as that of the Airbus A380); the noise level of the propeller drive; the aircraft control system and a weight of the aircraft that was 12 t too high; in addition, the loading ramp was currently not capable of allowing a tank to roll into the aircraft without causing damage at the ramp-aircraft transition.
On February 3, 2009, it became known that Airbus was no longer absolutely committed to the realization of the project due to financial problems caused by the increased financial requirements resulting from the technical problems and the program delay. Furthermore, according to industry circles, Airbus simulations had shown that steep approaches - also known as the "Sarajevo Approach" - would trigger propeller flutter with the current state of the art. Due to the serious technical problems, the long delay of the entire project as well as the high cost increases, neither a cancellation of the project nor an alternative planning was ruled out in the political discussion.
On 24 July 2009, however, the defence ministers of the countries involved agreed to stick to the project for the time being and to reschedule funding and deadlines within six months. A delay of four years compared to the original planning was expected.
In January 2010, the exact additional costs were unknown. Der Spiegel spoke of about 11.3 billion euros, about half of which was said to be due to problems with the engines. Other press reports speak of 5 billion euros. Originally, Airbus wanted to have the engines developed more cost-effectively by the American world market leader Pratt & Whitney Canada. However, European countries insisted on buying from a European consortium, which had to start a completely new development. As a result of this decision, Airbus considered the ordering states to share responsibility and threatened to cancel the project if they had not agreed to contribute to the additional costs by the end of January 2010.
Despite the high additional costs, the states and the aviation group EADS agreed to build the aircraft at the beginning of March 2010. The states were to agree to a price increase of ten percent (about two billion euros). They provided a further 1.5 billion euros, to be repaid by Airbus in the event of additional export sales of the A400M. A total of five aircraft were earmarked for the flight test programme, which are to fly a combined 4370 flight hours (Fh) (of which 1850 Fh for civil, 2520 Fh for military certifications).
On 5 November 2010, it was announced that the financing of the A400M had been secured. EADS had agreed on a solution for the military transport with the seven buyer states:
- Germany orders 53 instead of the planned 60 aircraft; the remaining seven orders are converted into an option.
- The German Armed Forces will forego the A400M's required fully automatic low-level flight capability. "These measures compensate for the German share of the price increase of around 670 million euros."
- Series production of the urgently needed machines should start towards the end of 2010.
- France should get its first machine in 2013.
- Delivery of the first aircraft to the Bundeswehr was scheduled for 2014. All aircraft for the German Air Force are to be delivered by 2020.
Production of the first series aircraft began at Airbus in Bremen in November 2010. The Armée de l'air planned to declare a first operational readiness after receiving the seventh aircraft, which would have been the case in 2014 if delivery had been made without delay. On 23 November 2011, Airbus Military announced that final assembly of the first aircraft destined for France (MSN007) had begun. The day before, the fuselage had arrived in Seville. Wings and the nose section had already been at the Spanish production site of the Airbus subsidiary since 26 October 2011.
Due to cracking of fuselage parts made of a certain aluminium alloy, Airbus announced to its customers in May 2016 that these would have to be replaced on all aircraft already delivered. The rebuild is estimated to take seven months per aircraft and is to be bundled with regular overhauls and retrofits where possible. In addition, damage to the propeller gearbox became known, which requires unscheduled maintenance during flight operations and which the manufacturer intends to remedy with the replacement of components and an "adaptation development" of the gearbox.
Flight test
Five prototypes are used for testing and certification of the aircraft. Prior to the first flight in December 2009, Airbus envisaged 1850 flight hours for this fleet to achieve civil certification, and a further 2520 flight hours to achieve military certification and entry into service, then scheduled for the end of 2012. Almost nine years after the first flight, Airbus announced in November 2018 that 10,000 hours have now been achieved in the ongoing flight test.
First flight
The maiden flight took place on 11 December 2009 in Seville and lasted 3 hours and 47 minutes. The take-off weight was 127 tonnes, of which 13 tonnes was test flight equipment and 2 tonnes was water ballast. On board were chief military test pilot Edward Strongman, test pilot Ignacio Lombo, flight engineer Jean-Philippe Cottet, responsible for the engines, flight engineer Eric Isorce, responsible for the onboard systems, and flight engineers Didier Ronceray and Gerard Leskerpit. The take-off took place at 10:15 a.m. (CET). After a flyover in landing configuration, the landing took place at 14:02. During the first flight, one of the control computers for the engines detected a failure, so one of the four engines was automatically put into neutral for safety reasons. The problem could possibly have been corrected by restarting the engine; however, since the aircraft would have landed with a stationary propeller if the restart had failed, this was not done.
Operation on unpaved roads
With its twelve-wheel main landing gear, the A400M is expected to achieve a better Aircraft Classification Number, i.e. a lower load on the flight operation surfaces, than the lighter C-130 with only four-wheel main landing gear. As of December 2016, the A400M was certified to operate on grass runways, while the certification process was still ongoing following tests on gravel and sand runways.
During a series of tests in the summer of 2013, the second prototype with the registration number EC-402 completed 25 landings as well as taxiing tests and aborted take-offs on a gravel runway near Ablitas in northeastern Spain. Certification tests involving some 40 take-offs and landings, as well as ground manoeuvres on grass runway and exposed earth, took place in September 2015 at Écury-sur-Coole in France. In May 2012, tests on the grass runway of the Cottbus-Drewitz airfield had to be aborted after the left landing gear sank into the grass during a take-off abort manoeuvre.
Tests on a sand runway were conducted by Airbus in August 2016 at the specially prepared Woodbridge Airfield in England. The French Air Force undertook a test campaign with its own aircraft on a laterite runway in Madama, Niger in August 2016. It found that increased repair work by pioneers was needed to remove ruts after A400M landings and make the runway usable again for smaller transport aircraft. A Royal Air Force aircraft landed and took off for the first time on a designated section of beach near Pembrey in Wales in 2017.
Air refueling capability
During a test flight on 5 December 2013, air-to-air refuelling was carried out for the first time, with fuel being delivered from a Transall C-160 to an A400M. The first "dry" test had been conducted in 2010. Further tests with the A400M as a tanker took place in August 2014, during which 68 "contacts" (docking manoeuvres at the tanker) were carried out and a total of 18.6 tonnes of fuel were transferred in 35 manoeuvres. In February 2015, fuel was delivered to two aircraft simultaneously for the first time during flight tests.
Whether the promised capability for aerial refuelling of helicopters, demanded by France, could be realised was not yet foreseeable by the end of 2015. In order to maintain the safety distance between the helicopter rotors and the aircraft, the refuelling hoses on the A400M have to be extended further from the tanks attached to both wings than on the shorter Lockheed KC-130. This increases the tendency for the hoses to become unstable. In addition, there is severe turbulence caused by the wings. France provided funds to purchase other tankers for this purpose. Airbus awarded a research contract to the ONERA institute to investigate the possibility of longer refuelling hoses, and initial wind tunnel tests were completed by mid-2016.
In 2019, flight tests for the certification of the Cargo Hold Tanks (CHT) air refuelling system were successfully completed. The A400M can carry two of the 7200-litre tanks in its cargo bay. The tests included the development and certification of the cargo hold tanks with the latest Fuel Quantity Management System software. The final certification is scheduled to take place before the end of 2019. Further work was done on the further development of the Night Tank Vision system and initial trials regarding helicopter air-to-air refuelling capabilities. In August 2020, a Eurocopter EC725 Caracal of the French Armed Forces was successfully refuelled by an A400M for the first time.
List of prototypes
Serial number | Identifier | First flight | Base | PlannedFlightHours | Testing areas |
MSN001 | F-WWMT | Dec. 2009 | Toulouse | 1200 h | First flight of the A400M, general flight behaviour, flutter testing, determination of acceleration limits. After 475 flights with almost 1445 hours, it was removed from the test programme on 4 November 2013 and parked. MSN001 has been on display at the Aeroscopia Museum at Toulouse-Blagnac Airport since July 2015. |
MSN002 | EC-402 | 8 Apr. 2010 | Sevilla | 1100 h | Testing of flight performance parameters, flights for civil certification, take-offs and landings on unpaved runways. |
MSN003 | F-WWMS | May 2010 | Toulouse | 0975 h | Tuning of the autopilot, tests with different fuel types and temperatures, testing of the hydraulic system and navigation systems, cold testing. Airbus announced in early November 2013 that MSN003 is no longer needed for the test programme. |
MSN004 | EC-404 | Jan. 2011 | Sevilla | 0870 h | Air-to-air refuelling, loading and carriage of cargo. |
MSN006 | F-WWMZEC-406 | Dec. 2011 | Toulouse | 0225 h | First aircraft almost in production condition, testing of the interaction of the components, consumption and reliability tests, tests on the electromagnetic compatibility of the systems, cold weather tests and development of the cargo loading systems. |
The machine MSN005, which is missing in the sequence, was not built. Originally, the test programme was to be carried out with six aircraft. MSN005 should have taken over flights at the end of the test programme to check the reliability of the systems. Airbus ultimately decided to use the first production aircraft (MSN007) for this purpose. With MSN056, an additional series-standard aircraft initially entered test and demonstration operations at Airbus in 2018.
Capability Standards
Envisaged capability standards (obsolete) | |||
militaryrelease | fully integrated capabilities | as of serial number | Year (approx.) |
IOC | Transport of troops, vehicles and military pallets of up to 32 tons in mass | MSN007 | 2013 |
SOC 1 | Airdrop (restricted) | MSN015 | Autumn 2014 |
SOC 1.5 | Departure from air self-protection air refuelling | approx. MSN032 | 2015 |
SOC 2.0 | Extended tactical application spectrumAdditional | approx. MSN045 | 2016 |
SOC 2.5 | Full air refuelling spectrum | approx. MSN090 | 2017 |
SOC 3 | Lowdown | approx. MSN120 | 2019 |
The Airbus A400M does not have its full range of capabilities from the outset. Rather, the first production examples were delivered in an Initial Operating Capability (IOC) version, a military qualification that initially enabled strategic airlift. As the serial number progresses, delivery is then targeted with Standard Operating Clearance (SOC), which expands the aircraft's tactical spectrum.
The Initial Operating Clearance required for the first delivery was granted on 31 July 2013. This contractually agreed standard was awarded by the Organisation for Joint Armament Cooperation (OCCAR), which issues the certificate on behalf of the launch customer states (Belgium, France, Germany, Luxembourg, Spain and Turkey).
The other plan targets could not be met. For example, the first German aircraft was not delivered in capability standard SOC 1 as planned. At the end of 2015, Airbus sought a renegotiation as some functions and capabilities were further delayed while others were ahead of schedule. In June 2016, France took delivery of the first aircraft intended for tactical missions with still limited self-protection, airdrop and aerial refueling capabilities. In February 2018, Airbus agreed in principle with customers to stretch out delivery and to allow individual negotiations to remove certain points from the specification that proved too difficult to implement.
Approval
Although the Airbus A400M was designed and developed primarily for military use, it is also certified according to the guidelines for civil aircraft construction; a circumstance that contributed significantly to the complexity of the development and to its cost.
Civil type certificate
On 9 May 2012, Airbus Military received the Restricted Type Certificate for the A400M from EASA. On 13 March 2013, the full civil type certificate was issued in accordance with the requirements of Regulation CS-25, which only covers the civil part of the project and does not include the transport of persons and loads in the cargo compartment.
Military approval
In order to harmonise the partly different certification procedures of the participating nations, the military components of the aircraft are tested by the joint Certification Qualification Organisation. Representatives of all partner nations belong to this organisation, for Germany representatives of the Type Certification Authority for Aircraft (ML) of WTD 61. On this basis, the individual nations issue their respective military type certificates. In addition, each individual aircraft has to be certified for traffic. The necessary quality assurance on the final assembly line has been delegated to the Spanish Directorate General of Armament and Material (Dirección General de Armamento y Material - DGAM). A Spanish Export Certificate of Airworthiness serves as the basis for the national military transport certification of the A400M.
The common basis for military certification was approved on 19 July 2013 on the recommendation of the Certification and Qualification Committee (CQC), composed of representatives of the seven launch customer nations. Accordingly, the French procurement authority DGA (Direction générale de l'armement) issued the French military type certificate for the A400M on 24 July 2013. The IOC approval of 31 July 2013 was the final step before the DGA certification of the first MSN007 production aircraft and the subsequent delivery of the aircraft to the French Air Force.
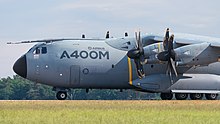

Side view of the A400M
_A_French_Air_Force_A400M_Atlas_performs_multiple_airdrops_at_Yakima_Training_Center.jpg)

Parachute drop of air cargo from a French A400M during exercise Mobility Guardian 2017.
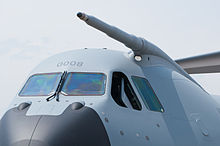

Air refueling probe above the cockpit
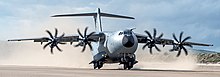

Take off of an RAF A400M from a beach in Wales
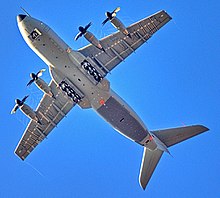

A400M on first flight (11 Dec. 2009)
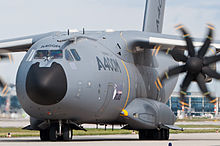

MSN004 at the ILA 2012
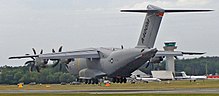

Prototype lands at the Farnborough International Airshow (2010)
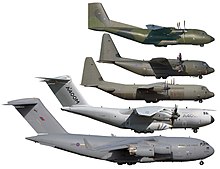

In size comparison to the A400M to be replaced or alternative types :- Transall C-160- Lockheed C-130- C-130J-30- Airbus A400M- Boeing C-17 (from top to bottom)
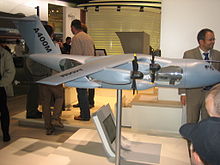

Model of the Airbus A400M (2006)

Rollout of the first Airbus A400M, EADS employees in the foreground (26 June 2008)
Construction
The Airbus A400M is a shoulder-wing aircraft with a T-tail and pressurised cabin. Thirty percent of the structure, including the wings (excluding the wing centre box), is made of composite materials. The fuselage is of conventional metal construction.
Cockpit and avionics
The A400M is equipped with a fly-by-wire flight control system. The cockpit is fully night vision compatible and provides space for the two pilots and an additional crew member for special operations. The cockpit is equipped with two head-up displays (HUD) and eight liquid crystal displays (LCD, 6 inches). Three screens for each pilot (primary flight display, navigation display and video display) and two common screens for surveillance and the flight management system. The HUD is certified as the primary display. The Flight Management System (FMS400) by Thales Avionics S.A. and Diehl Aerosystems GmbH is a further development of the flight management system from the Airbus A380. The optional EVS (Enhanced Vision System) for perspective terrain display on the screens is based on a forward looking infrared sensor. Automatic monitoring of flight parameters (Flight envelope protection) limits the maximum load in tactical operations to 3 g and the pitch angle in steep turns to 120°. The maximum roll rate of 30 degrees per second is twice as high as that of civil Airbus models.
Drive
Turboprop vs. Turbofan:
During the pre-development phases of the A400M, various technical solutions were investigated, particularly with regard to wing positions and propulsion concepts. Among the propulsion alternatives, turbofan and advanced turboprop engines were studied, each with two or four engines. The decision in favor of a turboprop engine with four engines was made for the following reasons:
- The lower fuel consumption of the turboprop engine compared to the turbofan engine (approx. 20 % less) results in a smaller fuel accommodation volume and thus a smaller and lighter aircraft. This reduces operating costs and improves maneuverability.
- With the turboprop engine, various tactical requirements could be better met (take-off and landing performance, steep descent, reverse roll, slow flight, faster response to thrust changes in low-level flight).
- The airflow accelerated by the propellers over the wings even at low aircraft speeds contributes to lift to such an extent that the lift aids could be constructed more simply and robustly and movable slats could be dispensed with.
- Less susceptible to damage from foreign objects on unprepared sites. The air intake is higher above the ground and is equipped with a foreign object separator.
These advantages, which are predominantly effective in the tactical operational spectrum, are offset by a lower flight speed than strategic transporters with turbofan propulsion, although the speed has been increased compared to the likewise propeller-driven tactical predecessor models.
Thrusters:
The A400M is powered by four EPI TP400-D6 turboprop engines developed in-house. Europrop International (EPI), a joint venture between European engine manufacturers Rolls-Royce plc, ITP, MTU Aero Engines and Snecma, was established to develop, manufacture and support the engine.
The three-shaft engine with bottom-mounted air intake has a rated power of 7971 kW, which is delivered to an eight-bladed Ratier-FH-386 controllable pitch propeller via a remote propeller gearbox made by Avio Aero. The propeller axis is offset upward relative to the engine shaft. The propeller has a diameter of 5.34 meters and is made of woven fiber composites. Due to the counter-rotating propeller movement, two different gearboxes and propellers are installed on each aircraft.
Technical data:
- Type: 3-shaft turboprop
- Starting power: 8251 kW
- Rated power: 7971 kW
- Compaction: 25
- Propeller diameter: 5334 mm
- Propeller rated speed: 842 min-1
- Propeller start speed: 860 min-1
- Mass: 1860 kg (dry)
- Length: 3500 mm
The performance of the engine is surpassed in the turboprop sector worldwide only by two engines, the relatively old Russian Kuznetsov NK-12 (installed among others in the Antonov An-22 and Tupolev Tu-95) and the Ukrainian Ivchenko Progress D-27 (installed in the Antonov An-70).
Control:
The engines are equipped with a FADEC (Full Authority Digital Engine Control) system supplied by BAE Systems and Hispano-Suiza, which also controls the propeller's angle of attack. The software was developed by MTU.
Direction of rotation of the propellers:
The two propellers of a wing rotate in opposite directions; clockwise as seen in the direction of flight at engines 1 and 3, at engines 2 and 4 the gearbox changes the direction of rotation. Thus the downward movement of the propellers takes place between both engines ("Down between engines", DBE). The airflow is symmetrical and concentrated in the center of the wing, enhancing lift and lateral stability. The propeller torque is balanced within the wings. Wing and tail unit can thus be designed more symmetrically. The yaw effect in case of failure of an outboard engine ("critical engine") is reduced. The vertical stabilizer, which has to compensate for this effect, can thus be made smaller. The principle is being applied for the first time on the A400M. The engines of the largest Russian and Ukrainian propeller-driven aircraft, on the other hand, have two counter-rotating propellers on the same hub, so that no counter-torque acts on the wing structure. On the C-130 Hercules, all propellers rotate clockwise.
Auxiliary power unit:
The auxiliary power unit (APU) and other components of the emergency power supply such as the Ram-Air turbine are supplied by Hamilton Sundstrand. The APU is located in the upper part of the fuselage in the rear right wing root.
Cargo hold
Rheinmetall Defence Electronics supplies the Loadmaster Control System. The system consists of a workstation and eight sidewall lock panels. The load compartment can carry up to nine standard military pallets (2.74 m × 2.23 m) together with 54 soldiers seated on either side, or up to 116 fully equipped soldiers or paratroopers in four rows. For a medical evacuation, 66 NATO standard medical stretchers can be accommodated with 25 medical personnel. Retractable wind deflectors are fitted in front of the side jumper doors for dropping paratroopers and to facilitate their exit from the laminar flow of the aircraft.
Self-protection
The self-protection equipment is put together individually by the operators. The components optionally offered by Airbus for this purpose can be supplemented by those procured by the operators themselves. In addition to an inert gas system for the aircraft tanks and ballistic protection for the crew, including bulletproof cockpit windows, decoys and electronic self-protection measures in various stages against enemy air defence are possible, but not included in the basic model of the A400M.
_Aircrew_members_prepare_an_A400M_Atlas.jpg)

Cargo hold


Europrop TP400 engine at the ILA 2012
.jpg)

Europrop TP400 engine
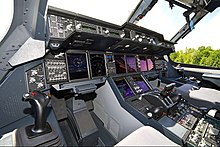

Cockpit of an A400M
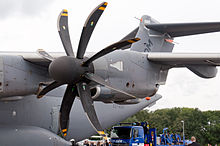

Propeller and engine of the Airbus A400M