Wire
This article discusses metal and plastic wire. Other meanings: Wire (magazine); for others, see Drath (disambiguation).
Wire is usually a thin and long shaped, flexible metal with often a circular cross-section. Other cross-sectional shapes show flat, square or profiled wires. Fine wire is usually wound on reels (spools, reels, spindles), while stronger wire is held in coils. Rarely, the term "plastic wire" is also used for stronger plastic filaments.
Metals that are often used in wire production are iron, copper, brass, aluminium, silver, gold, titanium and stainless steel as well as various copper alloys. In smaller quantities, magnesium is now also processed into wire and is used as a biomaterial or in the automotive and aerospace industries.
Cored wire is metal wire with a core of flux. Mostly it is brass wire for brazing, whose C-profile leg encloses the flux powder relatively tightly by compressive rolling, more rarely it is welding wire. Wire solder, in which one, rarely several channels with flux filling run, is only very rarely called cored wire.
Polymer monofilament with some stiffness can also be called wire. Nylon wire is used in decoration and for threading jewellery chains, PE wire is used as piping, PVC welding wire is used for joining PVC floor tiles.
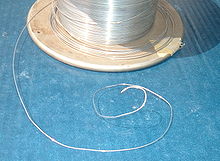

Stainless steel wire on a spool
Typology for metal wires
Designation according to diameter d | |
Steel wire drawing | Non-ferrous metal wire drawing (NF metal) |
|
|
Manufacture
Wire drawing is a process used since the Middle Ages in which coarse wire is drawn through a small opening in a tool, making it thinner and longer. In manufacturing technology, wire drawing is the most important application of drawing through. The wire drawer existed as an independent profession.
In production, a distinction is made between cold drawing, rolling and electrolytic treatment. In wire drawing, a coarse wire previously produced by forging, nowadays by rolling, is cold drawn through the tapering opening of a drawing die, drawing block or rolling stand. It becomes longer and thinner without any loss of material. From one production step to the next, it is drawn through smaller and smaller openings until the wire finally has the desired dimension - usually round. Originally, wire was drawn by muscle power, in a physically strenuous job to which there was no alternative until the late Middle Ages.
In industrial production, the wire is drawn through the die by a so-called drawing capstan. Modern wire drawing machines (multiple drawing machines) have up to 31 stages and are very demanding in terms of control technology, as all the drawing stages are run in a sequence.
Drawing is a plastic deformation and, if carried out cold, leads to work hardening. Therefore, heating (stress-relieving annealing) must often take place between the drawing stages. Wires made of copper have an important special feature here. After reaching the final strength (approx. 450 N/mm²), this type of wire can be further drawn almost at will without intermediate annealing. This means that copper wires can be drawn from the casting wire (e.g. 12 mm ø) to the finished product without heat treatment. Whether the wire is delivered hard or soft annealed depends on the application.
Drawing dies are often used for drawing metal wires. These are usually round and have an opening in the middle. The wire first runs through the inlet cone, which compensates for the offset to the previous drawing die or to the manual feed. The wire is then tapered in the reducing cone and work-hardened in the subsequent calibration zone. Finally, the wire runs out of the run-out cone, which compensates for the offset to the take-up reel or to the next drawing die. The drawing die heart, also called drawing core, used to be made of hardened steel or HSS (high-speed steel), today it is made of carbide, PCD (polycrystalline diamond, artificial diamond) or natural diamond. As these materials are brittle and as a tensile pressure load occurs during wire drawing, it is necessary that the drawing heart is set in a socket made of steel or stainless steel (VA).
The geometry of the drawing core is adapted to the material and the drawing process in several aspects. The length of the contact and forming zone and the opening angle of the cone define the degree of deformation that the wire undergoes in a drawing die. The opening angle is usually between 6° and 8° and the degree of forming between 10% and 90% due to the reduction in cross-section from
to .
The wire is drawn either by wet drawing or by dry drawing. In wet drawing, the wire is wetted with drawing agent or oil. This process reduces friction in the drawing die, keeps the wire cool and thus reduces work hardening. This results in better wire surfaces and allows for higher drawing speeds. Since the machine must be made liquid tight, it is often more expensive. The wire often needs to be dried before it is further processed or sold. It is also possible that the wire reacts with the drawing agent or oil.
A water-oil emulsion with about two percent oil content is often used as the drawing agent. In smaller quantities, drawing wax is also used, which reduces friction under the influence of pressure and temperature in the drawing die.
Square wire/profile wire
A special form of wire is the square wire or profile wire. This wire has a square or rectangular cross-section and is usually made from round wire. The tools used to produce square shaped wire are called turret heads and consist of four rollers (rolls) arranged symmetrically at right angles to each other, which exert a uniform forming pressure on the wire as it passes through them from four sides.
The name "Turk's head" refers to the arrangement of the rollers (drag rollers), which are arranged like a Turk's head knot, i.e. like the knots of the headscarves (turbans) traditionally tied in Turkish culture.
Customers for these square wires, which are mainly made of copper alloys, include manufacturers of press-fit connectors, who cut short pins from the square wires and install them in plugs and connectors.
Often this square wire is electroplated with tin or precious metals.
Other examples of profiled wire are overhead contact lines (grooved contact wire).
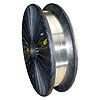

Electroplated square wire on a spool (roll)
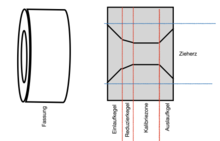

Drawing die in the cutting model
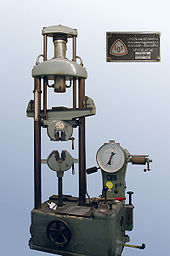

Older mechanical tester for tensile and compressive loads on wires
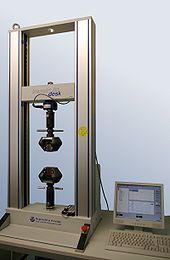

Computer-controlled tensile strength test