Wear
This article deals with the wear and tear of nonliving material. For the medical term see degeneration
This article or subsequent section is not sufficiently supported by evidence (e.g., anecdotal evidence). Information without sufficient evidence may be removed in the near future. Please help Wikipedia by researching the information and adding good supporting evidence.
Wear refers to the progressive "loss of material from the surface of a solid body caused by mechanical causes, i.e. contact and relative movement of a solid, liquid or gaseous counterbody", i.e. the loss of mass (surface erosion) of a material surface due to abrasive, rolling, impacting, scratching, chemical and thermal stress. In common usage, wear is also equated with other types of wear.
This usually undesirable change in the surface occurs, for example, on bearings, clutches, gears, nozzles and brakes, as well as wear on cutting tools. In the same way, the tyres of cars have to be changed regularly due to tyre wear. Wear changes the geometry of components so that they change their function. This results in component damage and the associated failure of machines and equipment. Reducing wear is therefore an essential way of increasing the service life of machines and equipment and thus saving costs and raw materials. On the other hand, attempts are being made to limit unavoidable wear to easily replaceable components, which are grouped together under the term wear part.
The wear behaviour can often be predicted. However, the procedures for determining service life must be distinguished from obsolescence.
The science of friction and wear as well as lubrication is tribology.
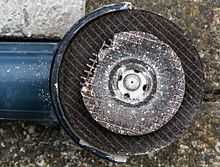

Worn cutting disc (front) of an angle grinder after freehand cutting of stone slabs (behind it the clamped unused tool)
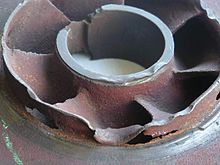

impeller of a pump worn out by cavitation
Influencing variables
- Basic body (material, shape, surface)
- Intermediate (type, particle size, etc.)
- Counterbody (material, shape, surface)
- Load (magnitude, time course)
- Type of movement (gliding, rolling, pushing)
- surrounding atmosphere (e.g. air, inert gas, vacuum)
- Temperature (altitude, time course)
Wear is always a system property, not a property of the components involved: There are always (at least) two components in interaction, often still an intermediate medium (fluid). In contrast, material fatigue and chemical ageing are also possible without the involvement of a second component.
Mechanisms
Wear is mainly determined by four different wear mechanisms:
Adhesive wear
Adhesive wear occurs in the event of insufficient lubrication. If components in contact lie firmly on top of each other under high surface pressure, the contact surfaces adhere to each other as a result of adhesion. During sliding, particles of the surface layer are sheared off. This results in holes and scale-like material particles, which often adhere to the sliding surface of the harder partner. This wear mechanism is called adhesive wear.
Example:
Protective oxidation layers are broken through as a result of adhesion due to the high local pressure at individual surface roughness hills. This results in local micro cold welding. Due to the strain hardening, the material does not subsequently
crack in the area between the two welds (fusion zone), but in the adjacent areas.
Abrasive wear
When hard particles of a lubricant or roughness peaks of one of the friction partners penetrate the surface layer, scoring and micro-chipping occur. This wear is referred to as abrasive wear, furrow wear or erosive wear - the latter can also be caused by fluids. The material loss caused by abrasion is called wear.
To prevent abrasive wear, lubricants should be monitored and replaced if necessary. In principle, abrasive wear can already be prevented during the design of a tribological system. Instead of metallic pairings, metal-plastic or metal-ceramic pairings should be preferred. As a general rule, in the case of metallic pairings, a favourable ratio (e.g. hard carbides in a tough intermediate material) between strength and toughness should be aimed for.
Abrasive wear plays a special role in systems in which media are conveyed that contain angular, hard particles. For example, abrasive wear plays a role in pipelines and pumps through which water with suspended solids (sand), plaster and concrete (aggregates) or filled plastic masses (fillers) are to be conveyed, for example in potting systems. In these cases, abrasive wear is a major cause of the shortening of the service life of components through which water flows.
Abrasive wear can be determined with a mechanical test method using the so-called Taber abrasor according to ISO 9352, ASTM D 1044 or DIN EN standard 438 - 2.6. In this process, wheels equipped with abrasive paper are pressed against the rotating surface of the test specimens with a defined pressure. The measured variable is usually the loss of mass of the specimen after a certain number of revolutions.
In the case where abrasive solids are suspended in fluids and cause wear, the term hydroabrasion is used.
Surface disruption
Surface disruption is a wear mechanism caused by alternating or swelling mechanical stresses. The result is a disruption of the surface, i.e. microcracks develop and grow in the material layers near the surface. Surface disruption occurs, for example, in rolling bearings due to constant overrolling. This wear, also called rolling wear, causes pitting. Since tensile stresses in the surface promote surface disruption, compressive stresses can be introduced into the surface as a countermeasure. Suitable processes are nitriding, oxidizing or shot peening of the surfaces.
Tribooxidation
The formation of intermediate layers, e.g. oxide layers, as a result of chemical reaction and their destruction by movement of the components is called tribo-oxidation or reaction layer wear. It almost always occurs together with adhesive wear. This wear mechanism, which occurs as a result of chemical reaction and mechanical destruction of the reaction layer, is a tribochemical reaction. An example of tribo-oxidation is fretting corrosion.
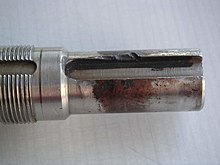

Tribooxidation (fretting corrosion) on a steel shaft
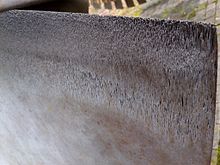

Erosion wear on a decommissioned low-pressure steam turbine blade
Questions and Answers
Q: What is wear in materials science?
A: Wear in materials science is the erosion of material from a solid surface by the action of another solid.
Q: What discipline does the study of the processes of wear fall under?
A: The study of the processes of wear falls under the discipline of tribology.
Q: How many principal wear processes are there?
A: There are four principal wear processes.
Q: What are the four principal wear processes?
A: The four principal wear processes are abrasion, adhesion, surface fatigue, and erosion.
Q: What is abrasion in wear processes?
A: Abrasion is a wear process where the material is removed due to mechanical action, such as rubbing or scraping.
Q: What is adhesion in wear processes?
A: Adhesion is a wear process where material is transferred from one surface to another due to friction.
Q: What is surface fatigue in wear processes?
A: Surface fatigue is a wear process where repeated cycles of loading and unloading cause cracks to form on the surface of a material, leading to material loss.