Two-stroke engine
A two-stroke engine is a reciprocating engine that generates mechanical power from the combustion of fuel. One cycle (one complete cycle) lasts one revolution of the crankshaft, i.e. two cycles. Like a four-stroke engine, it can operate as a gasoline or diesel engine. In everyday life, the colloquial term "two-stroke" refers to a valveless gasoline engine with mixture lubrication and spark plug(s) that operates according to the two-stroke principle; most two-stroke engines are simple and inexpensive, and they also have a low power-to-weight ratio.
Two-stroke engines were widely used in motorcycles, mopeds, scooters and the majority of karts. In passenger cars they were used, among others, in Trojan, DKW, Aero, Saab, IFA (Trabant, Wartburg, Barkas), Lloyd, Subaru, Suzuki, Mitsubishi and scooters. Two-stroke diesel engines were also available for diesel locomotives, trucks (for example Krupp Titan) and aircraft (for example Junkers Jumo 223).
They are now still used in outboard engines and portable equipment such as chainsaws, power scythes, lawn trimmers, leaf vacuums and leaf blowers, which are intended to be light and powerful and require engine lubrication independent of position. Two-stroke large diesel engines are used in power plants to drive electric generators and in ships ("marine diesel", for example Wärtsilä RT-flex96C), they are the largest and most powerful reciprocating engines and are among the most efficient heat engines.
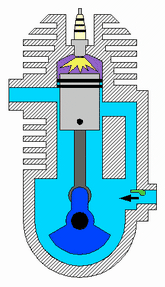

Schematic diagram of a transversely scavenged Otto two-stroke engine with diaphragm inlet
History of the two-stroke engine
Previous story
The first two-stroke engines, today called compressionless, worked on a different principle and are only called such because they ignited with every revolution of the crankshaft - just like the modern compressing two-stroke. In the first stroke, intake and uncompressed ignition took place, and in the second stroke the burnt gas mixture was expelled. The gas exchange was controlled by slide valves. Attempts by Jean Joseph Étienne Lenoir, Siegfried Marcus and others to use them for mobile purposes (between 1860 and 1870) failed, among other things, due to the unfavourable power-to-weight ratio of the engines. Carl Benz's "Sylvester engine" of 1879 also worked on this principle. The "stationary" two-stroke Benz system engine was built at the Mannheim Gasmotorenfabrik from 1881 onwards and produced in thousands.
Beginnings and technical development
Dugald Clerk is considered the inventor of the two-stroke engine. In 1878, in order to circumvent Nicolaus Otto's patent, he developed an engine with a separate scavenge pump that required only one crankshaft revolution per power stroke. This engine principle was first used to power a motor car in 1887 in the Petrol-Cycle by Edward Butler (1862-1940). Julius Söhnlein received a patent for the crankcase scavenge in 1891, in which the underside of the working piston acted as a scavenge pump piston. Like modern two-stroke engines, it had intake and exhaust ports. The overflow port opened into the top of the piston. At the same time Joseph Day developed a similar principle with a baffle plate on the piston, which he applied for a patent. In 1904 Alfred Angas Scott successfully designed a two-cylinder, two-stroke engine, and in 1908 he incorporated a more advanced version into a motorcycle. In 1909 he founded the Scott Motor Cycle Company, which manufactured two-stroke motorcycles until 1966. Hugo Ruppe further developed the two-stroke engine before World War I; his patents went to DKW, which produced the two-stroke engine in large numbers. In 1928, the Austrian manufacturer Titan developed the diaphragm control. Adolf Schnürle's patented reverse scavenging system, which replaced the cross-flow scavenging system and the nose-piston two-stroke from 1932, is considered a major development step. Daniel Zimmermann developed the rotary plate valve in 1952 and Yamaha the exhaust control in 1978.
Advantages and disadvantages of the method
Until the 1950s, the two-stroke engine was also considered to have a great deal of development potential for passenger cars and trucks. In many areas, the two-stroke engine had particular advantages:
- Higher maximum torque, in motor vehicles therefore potentially greater acceleration capacity than four-stroke engines with the same displacement
- More even torque output, as it fires twice as often per revolution as a four-stroke engine ("3=6" advertising by DKW)
- In the simplest case, only three moving parts: piston, connecting rod and crankshaft, thereby
- low-maintenance and reliable operation. The valve timing of historical four-strokes was extremely maintenance-intensive and thus an argument for the two-stroke. However, due to continuous improvements in valve timing, this aspect became less important over time.
- low weight
- No engine oil change required
- Very short warm-up phase, better cold start behaviour
- Low nitrogen oxide raw emissions
- Position-independent use with mixture lubrication, which is particularly advantageous for mobile implements
However, it turned out that many principle-related disadvantages of this engine design could not be eliminated. The main points include:
- Gas exchange: Only a short time around bottom dead center is available for expelling the exhaust gas and filling the cylinder with fresh gas. Four-stroke engines, on the other hand, operate two power strokes as a piston pump, pushing out the exhaust gas in one stroke and sucking in fresh gas in the following stroke. Two-stroke engines need their own scavenging blower, usually a piston blower, to do this. (Blower stands for a device for transporting gases at negligible pressure gradient). Crankcase scavenging is common in small gasoline engines, where the piston acts as a scavenging pump with its underside. In the case of multi-cylinder engines, this may require gas-tight separation of the individual crank drives. An alternative is scavenging with external blowers, which usually operate with rotary pistons (typically as Roots blowers or rotary vane pumps). The task must already be fulfilled at start-up, so that turbochargers, which need hot exhaust gases for propulsion, must be supported for start-up, for example by an electrically driven start-up blower.
- Scavenging losses occur because exhaust and fresh gas can mix during the charge change, which could result in fresh gas entering the exhaust or exhaust gas remaining in the cylinder. The resulting consumption disadvantage can be significantly reduced by direct fuel injection. Without direct injection, there is a conflict of objectives between residual gas and scavenged fresh gas, see also degree of capture. As a result, the fuel consumption of two-stroke gasoline engines with carburetors is comparatively high, so that only two-stroke engines with a maximum of three cylinders and 1.2 liters displacement were used in passenger cars. An exception was the Aero 50 with a four-cylinder two-stroke engine and a displacement of 2 litres; its fuel consumption is given as 12-16 l/100 km. The DKW 4=8 also had four cylinders, but the largest version had a displacement of 1054 cm³. The V6 two-stroke engine designed by Hans Müller-Andernach did not go into production and was only subsequently fitted to some Auto Union F 102s. This engine had a displacement of 1288 cm³.
- Loss of stroke: Compression does not start until the piston has closed both intake and exhaust ports. The four-stroke can start compression from bottom dead center, except for gas dynamics or special cycles like Miller or Atkinson.
- Thermal load: Due to the higher number of power cycles and the energy conversion, higher heat flows occur for the cylinder, piston and piston pin, which can be reduced by cooling or lower power, for example. However, piston cooling with splash oil is specifically opposed by crankcase scavenging (also: crankcase scavenging). If the exhaust gas is blown out via slots, higher temperatures are reached at the sliding surface of the piston rings and at the lubricating film than in a four-stroke engine. The problem increases because in the two-stroke engine considerably more heat must be dissipated via the piston than in the four-stroke engine.
- Mechanical and electrical stress: The piston rings in particular are at risk in the area of the inlet slots. Due to the fact that the piston and bearings are constantly under pressure, it is more difficult to maintain the separating lubricating film. In a four-stroke engine, the direction of pressure on these components changes when they are pushed out and sucked in, so that oil can flow into the gap by itself. Because the ignition frequency is twice as high, the ignition system is subject to particularly high stress and therefore also susceptibility to failure, especially in high-revving engines. The wear of the spark plugs is significantly greater.
- Oil supply: In a crankcase flushing system with minimized lubrication, rolling bearings must be used instead of plain bearings to ensure lubrication reliability. This means foregoing the advantages of plain bearings, which cause less mechanical noise and fail less frequently than ball bearings.
- Timing: The control times cannot be changed for control slots.
- Overall height: If the control slots are closed by the piston, a longer piston skirt and a correspondingly longer cylinder must be provided. In order to be able to continue to use a plunger piston, the connecting rod must also be made correspondingly longer. In practice, a four-stroke engine can be built more compact than a two-stroke despite the valve timing.
- Exhaust gases: The mixture quality is more difficult to control at λ=1 than in the four-stroke engine because of the requirement for safe flammability. Therefore, catalytic reduction of pollutants (KAT) in the exhaust gas is more difficult. Since the control slots are located in the lubricated cylinder bore surface and, with mixed lubrication, the oil supply can be adjusted less precisely to the actual requirement, two-strokes carry more oil than four-strokes in the exhaust gas. The result is a high amount of HC in the exhaust gas (30 times greater in the Trabant than in a comparable four-stroke).
- Smooth running: Smooth engine running only under load. When idling, the engine runs unevenly due to high residual gas content in the combustion chamber. In overrun operation, irregular ignition (so-called sliding jerking) often occurs (if no overrun cut-off is installed). Some two-stroke vehicles are equipped with a freewheel that prevents overrun.
- Braking force: The two-stroke engine develops less engine braking force in overrun mode. In the case of a non-locking freewheel, the engine braking force cannot be used at all.
Since low fuel consumption and good exhaust gas values are required in many areas of application, the range of application of two-stroke engines has been reduced to a few areas.
The two-stroke process was not able to establish itself successfully in automobile construction; in the course of the 1950s/60s, automobile manufacturers such as Saab, Suzuki, Mitsubishi and DKW had dropped the two-stroke process. The two-stroke engine was retained for a particularly long time in automobile construction in the GDR; as late as 1962, the GDR considered itself to be the domain of two-stroke engine construction and was full of expectation that it would still be possible to overcome the principle-related disadvantages of this engine. This was not successful, and yet the two-stroke engine was retained, so that the vehicles built until 1990, the Trabant 601 and Barkas B 1000, were the last series-produced passenger cars and trucks with two-stroke engines in the world.
The two-stroke engine had a longer life in motorcycle construction. Many motorcyclists were not bothered by the noise and exhaust emissions or the uncultivated idling behaviour. In motorcycle racing, the two-stroke engine showed its principle-related advantages over four-stroke machines. From 1994 onwards, legal bans for reasons of air pollution control displaced the two-stroke.
The two-stroke engine has survived in areas of application where independence of position, simplicity and low power-to-weight ratio are important. These include small mobile tools, boat engines, jet skis, microlight engines and small engines (model making). Furthermore, large two-stroke diesel engines are the most efficient power engines and are used in ships. The only thing that counts here is economy, as exhaust emissions in shipping are still hardly regulated by law.
Current developments
Efforts are still being made to overcome the scavenging loss and exhaust gas problems of the two-stroke process in order to make its advantages over four-stroke engines more widely available again.
Motorcycle manufacturers such as Betamotor, KTM, GasGas or Husqvarna offer two-stroke petrol engines for their modern off-road sports vehicles. At KTM, these are now exclusively direct-injection engines (reverse scavenging design). This keeps scavenging losses within limits, making the engines more efficient and cleaner. In addition, the Envirofit International project has been in existence since 2007, in which conventional two-stroke engines are converted to orbital direct injection in order to achieve more environmentally friendly exhaust gas values. This is achieved by replacing the cylinder head and retrofitting an injection system (kit). The goal of this project is to convert the millions of light motorcycles found in Asia with conventional two-stroke engines and corresponding environmental problems into more environmentally friendly vehicles. Other examples include BRP Rotax engines, which became more environmentally friendly thanks to a direct injection system (Ficht FFI), as well as the Rotax series, which are also used in Ski-Doo snowmobiles. Tohatsu builds two-stroke engines with the TLDI system (Two stroke Low pressure Direct Injection) for boats, Yamaha has the so-called HPDI system (High Pressure Direct Injection).
A number of small companies have developed, or are in the process of developing, workable opposed piston engines to harness their potentially lower fuel consumption. Unusually, the pivotal engine design, with water-cooled pivotal pistons and direct injection, allows scavenging losses to be kept to a minimum and mixtures of up to 1:300 to be used compared to conventional piston arrangements (typically 1:50-1:100).
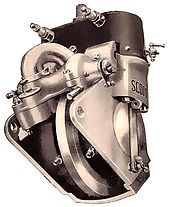

Scott two-stroke engine from 1912
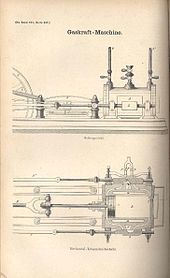

Compressionless, direct-acting two-stroke gas engine by Lenoir (1861)
How it works
Two-stroke engines, irrespective of their design and cycle, implement the process described below; the description begins with bottom dead centre. The processes under the piston in two-stroke engines with crankcase scavenging are written in italics for illustration purposes. Larger diesel two-stroke engines have scavenging fans for gas exchange.
First cycle: Compression / Suction
- The upward movement of the piston compresses the gas (air or fuel-air mixture) in the cylinder. The compression increases the temperature and pressure of the gas. The heat exchange with the environment is low, the compression is almost isentropic.
The piston moving upwards increases the volume in the crankcase, creating a vacuum in the crankcase. As soon as the intake port is released from the carburetor into the crankcase, fresh gas flows in.
- In gasoline engines, the fuel-air mixture is ignited by a spark plug shortly before top dead center. It burns so quickly that the piston moves little further during the combustion time, the volume remains almost constant (isochoric heat supply). In the case of the diesel two-stroke engine, the combustion of the diesel oil that is only then injected takes a little longer, the pressure remains approximately the same (isobaric heat supply). In both cases, a high pressure is generated.
Second takt: Work / Precompression
- The hot gas expands and presses on the piston, which runs back. The gas cools down in the process; heat is converted into mechanical energy.
The downward moving piston compresses the intake fresh gas as soon as the intake channel is closed.
- Near bottom dead center, the exhaust port opens first and then the overflow or inlet ports. The exhaust gas escapes, first until the pressure has dropped below that in the overflow ports, and the remainder is purged out by the incoming fresh gas. Large diesel engines commonly have controlled exhaust valves and intake ports. Small engines are port controlled, which means the piston clears exhaust and intake ports in the cylinder. The fresh gas can be a fuel-air mixture or just air in direct injection engines.
When the transfer ports are opened, the pre-compressed fresh gas can flow from the crank chamber into the cylinder.
On the way of the piston to top dead center, inlet and outlet ports are closed again, the drain starts compressing again. For scavenging, the fresh gas (either mixture or air) must be under pressure. To generate this, either the crankcase and piston underside is used as a pump or an external charge blower is used. Exhaust gas turbochargers (on large diesel engines) are combined with auxiliary blowers, since at start-up or low load the exhaust gas is not sufficient to operate them with sufficient effect.
The ideal gasoline or diesel cycle only approximates the process in the engine, because the gas exchanges heat with the environment and combustion and gas exchange take a certain time. The deviations are described by the degree of quality.